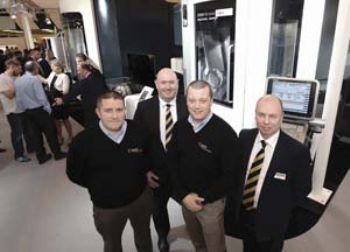
From a background of operating 14 three-axis machining centres, Kilkeel-based precision engineering firm Copas Technologies ordered a five-axis model from Coventry-based DMG Mori Seiki UK Ltd (
www.dmgmori.com) at MACH 2014 — following nearly three years of researching the market for the best five-axis partner.
Shaun Copas, owner and managing director of the Northern Ireland contract machinist, said: “This is a major milestone for our relatively young company, which was started in 2006. It is an investment that will enable us to maintain and improve our rapid-response support to customers and produce complex components quickly using 3+2-axis working and simultaneous five-axis machining. The DMU 60 eVo we ordered was exactly what we wanted, and we know that any further purchases will be right for our needs and budget.”
Mr Copas says that his company previously had to decline around one-third of the work on offer due to not having a five-axis capability. “Prototyping and the small-batch production of complex parts was not cost-effective to carry out on three-axis machines. “We are excited about the possibilities of growing our five-axis section and benefitting from all the traditional advantages, including fewer operations, better accuracy, less work in progress and lower expenditure on jigs and fixtures.”
DMG Mori also announced a new motor-sport partnership at MACH 2014. Under the motto “Mission 2014 — Our Return”, Porsche will return to the LMP1 class of the FIA World Endurance Championship (WEC) after more than a decade, with DMG Mori as the exclusive premium partner of the Porsche LMP1 team. The WEC consists of eight rounds on four continents and includes the Le Mans 24 Hours as the season’s highlight. On its stand, DMG Mori presented the 919 Hybrid, which marks the beginning of a Le Mans future featuring hybrid technology.
Meanwhile, the company’s Celos intuitive user interface for all high-tech machines from DMG Mori marks the beginning of a new era of what the company calls “seamless progression from idea to finished product”; the Celos interface was demonstrated on both the DMC 80 FD duoBlock and the NLX 4000BY 1500 multi-axis turning centre. Said to be as easy and intuitive to use as a smart-phone, Celos not only “simplifies and accelerates the process from the idea to the finished product”, it also forms the basis of
paperless manufacturing.
In addition, Celos Apps provides the user with integrated and digitised management, documentation and visualisation of order, process and machine data. Celos is also compatible with PPS and ERP systems, it can be linked to CAD/CAM applications, and it is designed to work with other Celos Apps, including Job Manager and Job Assistant, which support the machine operator with network-integrated planning, preparation, optimisation and systematic processing of new machining jobs. In all, 12 Celos Apps are currently available.
Other highlights included the fourth-generation DMC 80 FD duoBlock; with the Power-Master 1000 spindle and HSK 100 tool-holder interface in the B axis, this provides 77kW of power. Meanwhile, by adding vertical ultrasonic oscillations to the spindle of the Ultrasonic 20 linear, the company has made it possible to cut hard, difficult and brittle materials such as glass and ceramics, as well as carbon fibre, honeycomb stacks, and laminates of titanium and carbon fibre. Using DMG Mori-developed PCD tooling and oscillations of between 20 and 50kHz, feed rates up to 18m/min can be achieved, and finishing operations can be reduced through minimal burring and edge damage to laminated materials, making this technology extremely valuable for aerospace applications.