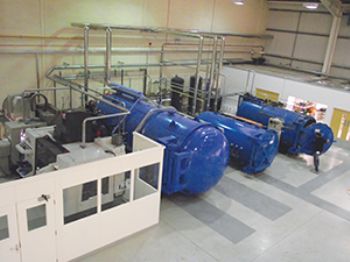
Brick Kiln Composites (
www.brickkilncomposites.com) is a long-established manufacturer of carbon fibre components for Formula One and sports-car teams.
As many as 50 of the company’s parts feature on a car, ranging from electrical trays to aerodynamic aids.
Oxfordshire-based Brick Kiln produces thousands of different parts a year using three autoclaves, a five-axis Haas vertical machining centre and a three-axis Bridgeport machine.
Moreover, the company is now looking to expand into manufacturing components for road cars. General manager Ronnie Dean says: “With fuel economy now being a priority, high-end vehicle manufacturers are incorporating lightweight composite components into their build, especially luxury car makers such as Bentley, Rolls-Royce, McLaren, BMW and Jaguar Land Rover. Indeed, all car manufacturers are seeking to make their vehicles lighter.”
In order to accommodate this new work, Brick Kiln is planning to build a mezzanine floor above the entire 12,000ft2 area of its facility and add new workshops to double its manufacturing capacity. The company will also be employing additional staff — and setting up a training programme.
Although Brick Kiln uses one of the most advanced techniques for making composite components — ‘pre-preg’ carbon fibre reinforcement that is cured under heat and pressure to produce high-quality parts with a high structural performance — many companies will not even accept a quotation from suppliers that do not have ISO accreditation.
“We needed the ISO 9001:2008 quality standard for the manufacture of parts and accessories for road vehicles and their engines in order to be considered,” says Mr Dean.
“Thanks to our use of the Javelin production planning and control system, we were already operating to ISO standards, so our ISO audit only lasted two days. Javelin enabled us to demonstrate all our systems on-screen in the
office, proving our traceability, how we know exactly what is happening on the shopfloor, and who is working on which parts.”
He says Javelin (
www.javelin-mrp.com), which is part of the Vero Software Group, was a major factor in achieving ISO accreditation and will grow with the company, keeping it in total control of all its procedures. “Javelin is all set to play a vital role in our automotive business; it can support a company with 500 staff just as easily as it does a company like us, with around 20 employees.”
hop Floor Data Capture is used extensively throughout Brick Kiln’s manufacturing processes, with terminals sited in seven departments, including clean room, inspection room and trim shop. The Crystal Reports feature also proves invaluable in giving live updates on a component’s progress through the factory; this is of particular importance for motor-sport customers with short lead times. “We often receive a mould tool in the morning with the customer wanting the component the same day,” says Mr Dean.
Production manager Nick Brew says that as the company develops its automotive business, he anticipates needing to make full use of Javelin’s powerful production control functionality. In particular, he expects the ‘What if?’ finite and infinite integral scheduling capabilities to come to the forefront; these allow the same work load to be tested using various scenarios and manufacturing rules, and the results compared either graphically or in a tabular format. Based on a model of Brick Kiln’s own factory, the system helps to minimise work in progress, keep lead times to a minimum, improve delivery performance and reduce costs.
Works Order is a core element of Javelin, controlling the progress of work through the entire process, with a full set of monitoring and tracking routines ensuring complete visibility at every stage. Javelin has also improved Brick Kiln’s invoicing system, as well as the company’s overall traceability capabilities; invoices that were previously typed by hand are now generated automatically by Javelin — and quickly.
Mr Brew says that any query about delivered parts is easily resolved. “As soon as we need to find something, we can trace it extremely quickly with Javelin. We can also look back and see what materials went into a part, who made it and when it was made. We’ve got the full material history; everything about every component is on the Javelin database.”
The uncured pre-preg carbon fibre used by Brick Kiln Composites is ideal for the type of lightweight components that are becoming increasingly important to the automotive industry.
It is easy to handle, and it can be cut and laid precisely into detailed and accurate moulds, making the process suitable for producing complex parts. Furthermore, the ease and accuracy with which the material can be ‘templated’ and cut significantly reduce waste compared to other manufacturing methods.”