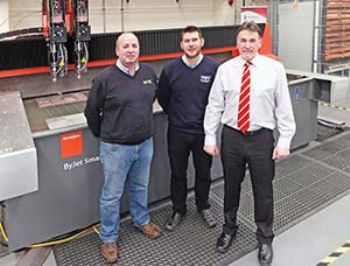
Established in 2012, Atom Fabs produces stainless steel, aluminium and plastic components for maintenance applications in the food industry; it also manufactures bespoke machines for the rotational moulding of plastic components.
Started by four engineers, the Chard-based company now employs 28 people and is working at full capacity.
Part of the reason for its rapid expansion is the formation of Westcountry Waterjet, a new division set up to provide cutting services to companies in Somerset and beyond.
The initiative was prompted by the purchase at the end of last year of Atom Fabs’ first water-jet cutter, a ByJet Smart 3015 twin-head machine from Coventry-based Bystronic (UK) Ltd (
www.bystronic.com).
This machine was needed to automate the production of profiles up to 25mm-thick required by the food fabrication section, as well as components made from steel up to 20mm thick for the division that manufactures the moulding machines.
Capable of processing sheet and plate up to 3 x 1.5m, the ByJet Smart was the right size for Atom Fabs; and because the machine has two cutting heads, its productivity was high. It was soon apparent that there was a lot of spare capacity — hence the decision to establish Westcountry Waterjet.
Lee Chant, one of Atom Fabs’ founders, established that there was interest from local firms: one needed composite materials profiled, another, while a specialist glass company needed 20mm-thick blanks cut in preparation for making periscope lens. Since then, a lot of additional work has been won, much of it requiring the cutting of plastics.
During a single day in March this year, three jobs were received. One involved cutting 100mm-thick military-grade PTFE into circular blanks for the customer to turn into seals; another required 25mm-thick adhesive-backed foam to be profiled for a cigarette manufacturing machine; and a third needed 25mm-thick aluminium and polycarbonate to
be profiled.
The new division has been so successful that three-quarters of the work on the water-jet profiler is now sub-contract jobs. To keep pace with the high work-load, the company has started 24hr operation, six days a week.
Components produced recently for in-house use include press-brake tooling made from 60mm-thick S355 steel.