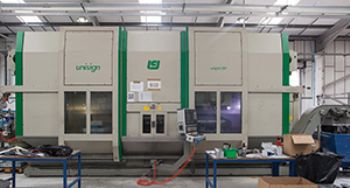
Founded in 1978, Hymec Aerospace Group provides precision-manufactured components predominantly for the aerospace industry, although it also has customers in the defence, medical, telecommunications and motor-sport sectors.
Moreover, its customer base is a global one, as is its operation: in addition to its main 85,000ft2 factory in Plymouth and a facility for design and development work in Newton Abbott, it has manufacturing plants in the USA and Thailand.
Initially, Hymec was a ‘make to print’ company, but around 20 years ago it introduced a plan for growth that has seen it develop partnerships with its customers, integrating all operations that allow it to ‘ship to stock’ many of the precision-machined components, sheet metal components and structural assemblies that it produces.
As a Tier One supplier to leading aerospace companies, Hymec works on short-, medium- and long-term projects based on processing a range of materials, from light alloys through to hard-to-machine alloys; the company also provides heat treatment, penetrative flaw detection and specialised finishing services.
Group director and co-owner Richard Elliott says: “In addition to our on-going programme of investment in machining technology, we also recognise that our people and systems are key to our success. Training and education are vital; our apprenticeship programme sees between seven and 10 apprentices taken on every year. Each of them is challenged to better themselves, and we give them the opportunities to do so.”
Throughout Hymec’s history, machining has been its core competence, with the bulk of its machining capability being developed in partnership with Leatherhead-based Matchmaker CNC (
www.matchmakermc.co.uk): Hymec currently has around 80 CNC machine tools at its main factory in Plymouth, and 65 of these were supplied by Matchmaker CNC.
This long-term partnership began in 2003 when Hymec bought four Mitsubishi MH5Bn horizontal machining centres to increase its machining capacity; it has since added numerous Fadal and Matchmaker Tongtai machines.
Following its acquisition of Harbourne Engineering, Hymec focused increasingly on the use of horizontal machining centres and began buying more of these — again from Matchmaker CNC. “We recognised that with multi-pallet horizontal machines, we could maximise spindle utilisation and increase productivity,” says Mr Elliott.
The first of these machines were Japanese Kiwa KH-45 400mm multi-pallet HMCs. While this machine type has been designed to grow with the user’s production needs, Hymec specified multi-pallets from the outset; the company also specified the option of a 220-tool ATC for each machine. With their 22kW 12,000rev/min spindle, these Kiwas are ideal for the light-alloy work undertaken by Hymec; the company has subsequently installed more of them.
More recently, Hymec has been tackling other areas of aerospace component manufacture, following a programme of investment that allows it to machine larger airframe components made from harder alloys — hence its acquisition of
a Unisign Unipro 5P from Matchmaker CNC.
This machine has a 2m-long bed (plus a pendulum machining option) and provides a full five-axis machining capability on a much larger scale than Hymec could previously offer.
Its installation was a step change for Hymec, but Matchmaker CNC developed a special training programme for the company’s staff, to ensure they could maximise the machine’s potential.
“The learning curve was a steep one, but the advantages that we have gained — and the new business we have already won — as a result of having the Unisign machine are extremely encouraging. Our longer-term plans will see additional Unisign machines being installed at Hymec,” says Mr Elliott.