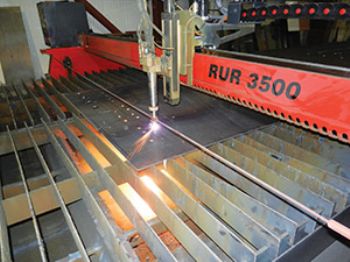
McGrath Engineering Ltd — a family firm based in Dungannon, County Tyrone — manufactures a range of tracked and wheeled conveyors, including the well-known Ezystak.
The company has seen its turnover grow by 300% (and its staff levels by 580%) in the last five years, and it recently invested in new equipment to keep up with growing demand and to eliminate the problems encountered when using sub-contractors to supply the profiles it requires.
This equipment included an RUR 3000 CNC UltraSharp plasma cutting machine from Lancashire-based Kerf Developments (
www.kerfdevelopments.com), followed by an RUR 3500.
Managing director Seamus McGrath says: “We wanted to eliminate the bottlenecks caused by suppliers delivering parts to excessive lead times, as this was putting pressure on other departments, and we wanted to reduce our production costs.
"We needed a reliable machine with excellent cut quality, and after reviewing the market, we selected the Kerf RUR machines — based on the build quality, the cut quality achieved with the UltraSharp plasma unit, the reputation of the supplier and the availability of local support in Northern Ireland.
"The first machine was installed along with a large press brake, and this was so successful that the decision was made to order a second machine and bring all the work in-house.”
McGrath Engineering specified each RUR machine with a 10m bed, so that it could cut 5 x 3m sheets at one end while loading or unloading a sheet at the other. The pendulum loading system increases machine output by up to 70%; combined with the speed and precision of the UltraSharp plasma system, which can cut mild steel from 3 to 35mm thick, this has reduced lead times by at least two weeks.
Mr McGrath adds: “We were spending upwards of £12,000 per week on sub-contract cutting. That has been eliminated, and we now offer our own sub-contract cutting service. The Kerf machines have been so influential that they will pay for themselves in the coming months on direct cost savings alone.”