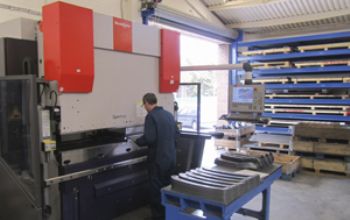
Folded parts are all around us, from filing cabinets and computer housings to cash registers and point-of-sale retail racks; and while it is easy to pass them by without a second thought, the reality is that production engineers will have agonised over establishing the most effective means of manufacture.
One commonly used forming method is press braking which, according to Luton-based Trumpf, Luton (Tel: 0844 482 0188 – www.uk.trumpf.com), comprises three main techniques. The first is ‘air bending’, the standard method for producing angles from 30 to 179deg, where the upper tool presses the workpiece into the lower die without actually forcing the material up against the inside of the die. As the tool is lowered, the flanges of the workpiece are turned up, creating an angle at the point where the tool meets the material. Trumpf says that air bending is used frequently because it is less costly and more flexible than other techniques. Moreover, the ‘low tonnage’ requirements of this method make it possible to employ smaller, more economic machines.
The second technique is ‘bottom bending’ or ‘coining’, whereby the tool presses the workpiece completely into the lower die until it is unable to move down any further. The machine control, however, continues to increase the tonnage, until the specified value is attained. The high pressure helps to stabilise the angle so that spring-back is almost completely eliminated. The tonnage needed for bottom bending is up to eight-times greater than that for air bending. Trumpf says that bottom bending is used primarily for producing 90deg angles on thin sheet-metal parts where small bend radii are required.
The third technique is ‘folding and hemming’ (to produce a ‘safe’ edge), which produces a bend with flanges that are parallel to each other. The folding and hemming are performed in two steps. First, the operator makes a bend of 30deg. Next, the workpiece is repositioned in the tool, and the machine flattens the fold. Folding produces a bend with flanges a certain distance apart, while in hemming the flanges are pressed together completely. Special tools allow both steps to be performed at a single workstation.
Correct tooling selection is vital for all types of bending techniques, and there are a number of factors to consider, including bend length, material type, sheet thickness, the length of the shortest leg of the bend, and the size of the bend radius (if the specified radius is less than the ‘minimum bend radius’, the sheet might tear on the outside of the bend or wrinkle on the inside; as a rule of thumb, the minimum bend radius should always be greater than the sheet thickness).
More variety
In economies such as the UK, where small batches and short deliveries dominate, set-up times are a key factor when it comes to selecting press brakes, as Wythenshawe-based electrical-equipment manufacturer Electrium (part of the Siemens group) confirms.
Engineering manager Graham Hodgkiss says: “Gone are the days when we were making 15,000 of the same thing. Today, customers want more variety in smaller volumes, so we can be processing orders for ones or twos one minute, followed by orders for 500 the next. As a result, we need equipment that is going to reduce the impact of set-ups.”
Until recently, five old press brakes were creating a real bottleneck at Electrium. The average set-up took 45min; and with around 50 set-ups a week, lost production time was high. However, following extensive market trials, the company bought two 100-tonne 3m-bed Easy-Form CNC press brakes from LVD Ltd, Banbury (Tel: 01295 676800 – www.lvdgroup.com), plus LVD CADMAN-B 3D off-line programming software. These machines were followed six months later by a 135-tonne Easy-Form.
When the first two press brakes were delivered, they were installed alongside two of the old machines, so Electrium was able to make a direct performance comparison. “We achieved a 70% reduction in set-up times, and I was surprised to learn that we also got a 10% reduction in run time,” says Mr Hodgkiss. “Some parts that previously took nearly an hour to set now take 10min — including programming. Also, because we are nesting components on cold-rolled sheet, we may be bending across the grain, with the grain or at an angle to the grain — all on the same sheet. This would have caused problems before, but the Easy-Form compensates for grain variation.”
Consistent bending
The days of the ‘little black book’ appear to be long gone when it comes to press brake operations, as demonstrated by Atherstone-based Tow-Trust Towbars, which recently installed a new Xpert 100-tonne 2,050mm press brake from Coventry-based Bystronic UK Ltd (Tel: 0844 848 5850 – www.bystronic.co.uk).
The Xpert is the ‘flagship’ of the Bystronic range, and among its features is the company’s Pressure Reference System, which automatically measures the true force required to form each bend. This measurement, carried out every 8msec, is evaluated by the CNC system and used to calculate — and compensate for — the deflection that occurs naturally within the frame of the machine. By combining this with the Xpert’s hydraulic lower-beam compensation, the control regulates the amount of crowning — deflecting the bed and table — and ensures that the fold angle is consistent along its entire length. Forming can therefore take place anywhere along the bed, which is particularly useful at Tow-Trust, where more than one tool set-up is often required for the same component.
Sub-contractors are also finding advantages in the latest press brake technology, as demonstrated by Stevenage-based Propak Sheet Metal, which in June installed seven HFEII CNC press brakes from Amada UK Ltd, Kidderminster (Tel: 01562 749500 – www.amada.co.uk). Andy Hughes, Propak’s sales director, says: “Our existing press brakes were around 15 years old, and although they continued to offer good service, technology has moved on. We needed to be taking advantage of that.”
Among the main features of Amada HFEII machines are the new AB Pad touch-screen control, which offers intuitive graphic programming backed up by fast processing speeds and high memory capacity. Bend sequence and optimised programming can be achieved in a simple step-by-step method, while an innovative ‘sketch mode’ enables users to draw a profile of the part and shorten the programming process even further. Other ‘smart’ innovations include ‘stop-start’ technology on the motors, which turn off when not being used and restart as soon as the pedal is pressed, offering energy consumption savings of around 50%.
Amada recently introduced its new HD press brake range, which provides users with high precision plus reduced running and maintenance costs, using the company’s new ‘eco’ hybrid drive system. This is complemented by two new automatic angle measurement systems (BIS and BIL), which both work with standard tooling and provide automatic bending compensation on material up to 12mm thick.
Set-up times
Assessing recent major installations, it is clear that the biggest factor in press brake selection is set-up time. Harlow Group, an Essex-based sub-contractor, is another company that confirms this, following its investment earlier this year in an E-Brake from Leicester-based Safan UK Ltd (Tel: 0116 200 1777 – www.safan.co.uk). Since the machine was installed, cycle times have been cut by 25-30%, while set-up times have been halved.
Manufacturing director Marc Boulden says: “Reducing set-up times is fundamental for our business. Batches are getting smaller, and lead times are getting shorter to meet increasingly shorter times to market. It’s no longer commercially viable to simply accept that a press brake takes a while to set up. We want to apply the Formula One tyre-change model to press brake operations — and the Safan E-Brake is the closest currently available.”
The E-Brake 35-1250 (35-tonne capacity ¥ 1,250mm bending length) features a patented ‘roller’ drive system in the upper beam to ensure a uniform and direct distribution of forces. This means that accurate and constant bending angles along the entire working length of the machine can be achieved without the need for crowning. The servo-electronic drive with fast start and stop times provides bending speeds of up to 20mm/sec. In addition, Safan says the machine consumes up to 50% less energy than machines using conventional drive technologies. “Today, deliveries of two weeks are a luxury, and inside a week is a frequent occurrence. In fact, more than 50% of our work is called off on a Kanban basis of daily deliveries. We don’t know what deliveries are required tomorrow, so our manufacturing processes have to be very responsive,” says Mr Boulden.
If set-up times are so important, then surely the versatility of the press brake is hard to surpass. Or is it? Vendors of panel-bending machinery beg to differ, dismissing the widely held perception that these machines are only good for large batches of tray-type components.
Steve Williams, the UK sales manager for Salvagnini UK & Ireland Ltd, Ross-on-Wye (Tel: 01989 767032 – www.salvagninigroup.com), takes up the argument. “The benefit that recent Salvagnini customers are profiting from is zero set-up time. With the auto tool change system, changing from job to job is done in ‘masked’ time, making small batch sizes no issue.
Traditionally, I think the market perception is that panel benders are really fast but you need to be doing large batches. In fact, the opposite is true today; small batch sizes are easy, due to machine flexibility.
“We recently sold a panel bender to a company that made a time comparison on seven typical parts with batch sizes of between one and six parts. They timed the whole process on the panel bender and one of their best press brakes. The times were 13min for the whole batch on the panel bender and 87min for the press brake — a 6:1 improvement in performance.”
Among recent purchasers of Salvagnini’s automated PX4 panel bender is Livingston-based Mitsubishi Electric Air Conditioning Systems Europe. The decision to buy this machine was made after tests on an existing press brake showed that it would be difficult to handle new larger-than-typical panels without damaging the pre-coated steel blanks.
Salvagnini says that the bending operation on a P4X panel bender is much safer than using a press brake, as the sheet is not moving up and down; this also means that bends can be completed far quicker. Furthermore, the PX4 was offered to Mitsubishi with the auto-blank holder to provide zero set-up time. This was important because the new panels are likely to be made in small batches.
According to another supplier of panel benders — Corby-based John Murray Machinery (Tel: 01536 772397 – www.jmmachinery.co.uk) — the latest RAS machines it sells in the UK are engineered to create parts ‘no matter how large’ with only one operator. This is because a panel bender uses an integrated support and back-gauge system that holds and manipulates the workpiece with minimal operator involvement — and it eliminates whip.
Additionally, when using RAS machines, no set-up or changeover is required when changing angles, material thickness or material types. Any angle from 0deg to 135deg — including open and closed hems — can be done with the same tools. Shimming is never necessary, and tool clamping is automatic.
Entry-level press brake
From an entry-level perspective, Durma’s AD-E series of press brakes from Axe & Status, Milton Keynes (Tel: 01908 647707 – www.axestatus.com), has been superseded by the new AD-R range — but with no increase in price. The AD-R series uses the same frame as the Durma ‘top range’ models and offers greater daylight (530mm), stroke (265mm) and throat depth (410mm) than the previous models. Bending lengths vary from 1,250mm on the 1260 model to 6,050mm on the 60400 model. The respective bending forces are 60 and 400 tonnes. The speed of movement through the axes is also much improved, and new CNC system options complete the upgraded package.
Particular highlights of the new range include: long double guides for easy and accurate moving of the top beam; CNC operation of the back-gauge in the X axis; easily adjustable sliding front arms for ‘finger tip’ lateral adjustment; Euro-style multi-V tool-holders with quick-release clamping; and manual or motorised crowning on all machines.
Small-batch folding option
According to Horley-based UK Machine Tools Ltd (Tel: 01342 313935 – www.ukmachinetools.co.uk), which sells Codatto panel-bending systems, the latest machines in the range accommodate low batch sizes (down to single items) and achieve an accuracy of ±0.05mm, while still giving high production rates, low manual-handling times and high levels of safety.
The ability to accommodate small batch sizes come from Codatto’s innovative tooling concept (which allows automatic tool changes between jobs), fast programming or program recall, and ease of angle setting accuracy using a patented camera system. Enhanced accuracy comes in part from the design for the movement on Codatto’s patented slideways, which reduce tolerance build-up and help maintain accuracy over a long period of time. The machines are specified for up to 3mm mild steel and up to 2.2mm stainless steel.