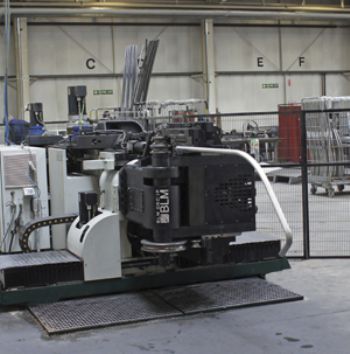
Having started life in September 1997 on a ‘one man and his apprentice’ basis, SJ McAuley Engineering is now a much broader-based business that encompasses precision machining and the manufacture of precision sheet-metal components. It is also equipped for MIG and TIG welding as part of a dedicated assembly process involving punched, machined and folded components.
Based in 74,000ft2 premises in Ballymoney, County Antrim, since July 2010, the 90-employee sub-contractor is the creation of managing director Jonathan McAuley. Since setting up the company in his mid-20s, he has invested heavily in the latest technology and the skills needed to satisfy the production demands of the company’s many customers.
“Quality control and flexibility are the keys to building and maintaining strong relationships,” he says. “That’s why quality and training are at the top of our agenda, with constant monitoring of both to ensure that our customers receive not only high-quality products but also a high-quality service. People don’t want to spend time and money checking our work, so they must be sure it is correct in every detail. The best way to convince potential customers that this will be the case is to introduce them to existing customers, because the majority of our work is down to word-of-mouth recommendations.”
Investment in the burgeoning sheet-metal side of McAuley Engineering began with a guillotine and press brakes, then a CNC punch press — followed (in 2007) by a BLM E-Turn 52 tube bender. This opened the door to work from the transport industry, supplying handrails for buses and other items such as radiator and air intake pipes. Three years later, a larger-capacity BLM Elect 80 CNC tube bender was installed; this has allowed the company to win additional work from the automotive industry as well as from the food, waste management and construction sectors.
Increased workforce
The net result, according to Mr McAuley, is that “recession has not had a major impact on this business. Indeed, since 2008 we have doubled the number of people employed here.” This achievement has not gone unnoticed: earlier this year (at the North Antrim Business Awards night), he was presented with the Entrepreneur of the Year Award to add to a previous award in 2008 for the Best Use of Technology. However, Mr McAuley is the first to acknowledge that success depends on teamwork and on all-round commitment and expertise, and this is one reason why the Northern Ireland sub-contractor has implemented its own apprentice-training programme.
General manager David Condell says ensuring it had an all-round expertise was also the reason why McAuley Engineering opted for the two BLM machines. “We were not involved with tube bending prior to 2007, but when we received an enquiry for handrails, Jonathan set about researching the market and available equipment. While we had little prior knowledge in this field, we knew what our customers required. We opted for BLM because there were very few suppliers at that time offering all-electric machines. Moreover, the E-Turn 52 offered high levels of accuracy and repeatability — plus left-hand and right-hand bending in the same cycle.
He adds that the E-Turn 52’s all-electric technology gives a 40-50% productivity increase when compared with ‘traditional’ powered models of bending machine. “It also has axis accuracies of ±0.05deg and ±0.05mm. Moreover, complex components requiring radii of 1 ¥ diameter or less can be produced using the ‘X-axis boost’ facility, which can apply up to 5,000kg at any point along the machine bed.”
Shorter set-up times

This level of performance, combined with precise control of the E-Turn’s 12 axis movements — courtesy of BLM’s Visual Graphic Programming (VGP 3-D) software — significantly shortens set-up times. All parameters are stored and can be recalled without any further mechanical adjustment; and because the electric axes adjust position automatically, accuracy and repeatability are enhanced. “Furthermore, components are produced ‘right first time’, and they are repeatable from batch to batch without undue reliance on operator expertise; and because all axis movements are set automatically, a job change-over can typically be completed within 2-3min.”
Mr Condell also says that, as with the BLM E-Turn 52, the larger BLM Elect 80 effectively de-skills the tube-bending process — previously so reliant on individual operator expertise. Furthermore, after a tooling change, the Elect machine initiates a single ‘machine protection cycle’, which runs at 20% of the normal speed and power. This ensures that, should a collision be caused by inadvertent operator error (fitting an incorrect clamp die or pressure die, for example), it will not damage the machine or tooling. The Elect also has a robustly built bend head and machine frame, while a compact integrated gearbox contributes to the much greater clearance area around and beneath the bend head. Unlike machines fitted with a fully external gearbox, this allows more-complex components to be completed in a single cycle.
Although pleased with the success of the on-going investment programme, Mr McAuley is keen to define ISO 9001-accredited McAuley Engineering as “more of a solutions provider than a machine shop”. This is a reference to the design expertise available in-house and to the focus on cost-effective design for manufacture — whether for the company’s sub-contract customers or for its own product developments.
“We have drawn up a new business plan in which we envisage further significant growth over the next three years, with capital investment continuing to be driven by our customers and by our own long-term requirements. There will be no change to our strategy, which has always been about buying top-end equipment, not least because it means customers can see for themselves that we are a professional operation using high-quality machine tools.”