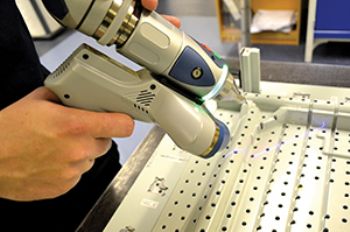
As it is critical that its car seats meet demanding customer expectations of comfort and craftsmanship, Sunderland-based Lear Corporation (
www.lear.com) applies a range of technical developments to ensure that its foam products meet strict automotive performance specifications.
Established to supply the nearby Nissan plant with seating systems on a just-in-time basis, Lear recently undertook a multi-million-pound investment to double its total capacity to more than 600,000 car seats a year.
Jim Handy, Lear senior quality engineer, says: “To enable the Sunderland facility to uphold Lear’s reputation for the quality of its car-seat foam products, stringent quality checks are regularly undertaken. As the correct dimension of car seats has an influence on their comfort, safety, durability and aesthetics, a wide range of measurements are made on foam components.”
Given the deformable nature of its foam products, Lear uses the non-contact scanning capabilities of the Faro Edge Scan-Arm HD (
www.faro.com) to ensure that accurate measurements can be taken.
“Following a Faro measuring routine, we use the data obtained for examining ‘significant characteristics’ and for inspecting sections through the component. In addition, we use the data for making precise CAD variance comparisons.
“A typical measuring routine consists of a fixture that precisely represents the surface of a foam injection tool used for production being accurately scanned and the captured data stored.
The foam seat component under inspection is then placed on the same fixture and aligned to duplicate its position at the time of manufacture.
A second scanning routine is then undertaken, and the results are saved as a point cloud. The original fixture datum point cloud is imported, along with the point cloud of the foam seat component. The relevant CAD model is then imported and displayed as a reference file, allowing a comparison to be made.”