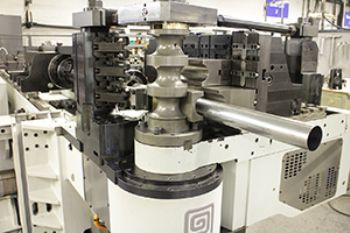
Janspeed (
www.janspeed.com), the Salisbury-based manufacturer of ‘performance’ exhaust systems, has significantly increased its tube-bending capabilities by purchasing a second Elect 80 all-electric CNC machine from BLM Group UK Ltd (
www.blmgroup.com).
This is the next step in replacing the hydraulic bending machines used by Janspeed to make the complex tube forms required for the exhaust systems that it supplies to prestigious customers in the OEM automotive sector.
The Elect 90 machines do not require the same high levels of manual skill, and they are more environment-friendly — using less energy and eliminating issues with hydraulic oil.
The combination of all-electric operation and touch-screen control also brings operating efficiencies, with Janspeed able to simulate jobs on the control while the machine is bending parts.
The simulation provides an accurate cycle time for quotation purposes and allows the company to optimise programs before they go into production. All parameters are set and managed via the tough-screen control, while the use of absolute encoders enhances accuracy and reliability — and reduces maintenance costs.
Both Elect 80 machines are being used on stainless steel tube of various lengths and up to 80mm in diameter, which was beyond the capabilities of Janspeed’s hydraulic bending machines.
Thanks to the nine axes of movement and having up to eight tools in the multi-stack tool system, it is possible to achieve multi-radius and variable-radius bending on the same tube in the same cycle. Compound bends can be produced, as well as bends with very little straight between them.
Mark Vaughan, managing director of Janpseed, says: “The first BLM Elect 80 at Janspeed was part of a major investment programme. The success of that first machine proved the viability of the all-electric system; the second machine confirms our commitment to maximising our manufacturing efficiency, product quality and overall service levels.”