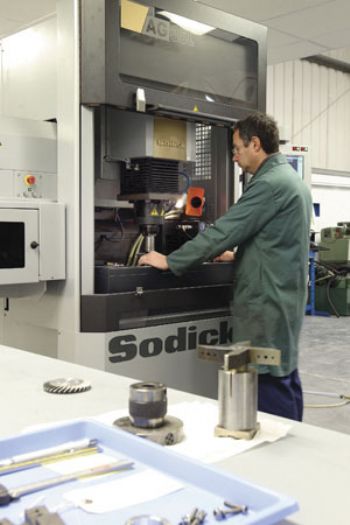
Coventry-based Bladon Jets (UK) Ltd — a global leader in the development and manufacture of small, multi-fuel, micro-jet gas turbine engines — is underpinning its patented breakthrough technology with two recently installed EDM machines. The company is currently participating in development projects with many leading automotive OEMs, and is aiming to power the cars of the future.
According to company director Philip Lelliott, Bladon Jets makes “disruptive technology” — a new innovation that is capable of transforming the automotive industry. The proprietary micro-jet engines developed by the company are lighter, less polluting and cheaper than conventional reciprocating combustion engines — a 100-year-old technology producing engines that are still used in almost all cars today. Furthermore, since gas turbine engines will run on just about any type of fuel, including LPG and bio-fuels, they are not dependent on dwindling oil reserves.
The immediate and near-future target market for these gas turbines is electric vehicles, which currently suffer from having a limited range. Using current technologies, users can only drive 80-160km before having to stop and charge the batteries. To solve this, an alternative power source is required. Modern hybrids (HEVs) combine electric power with traditional piston-driven car engines, but these are heavy, complex and can only operate using a single type of fuel — either petrol or diesel.
“By comparison, our gas turbine engines are very light — just 3kg compared to over 100kg for a piston engine. Moreover, they only have one moving part, not 2,500, making them simpler to produce and maintain,” says Mr Lelliott. “They are also efficient, green, offer multi-fuel capability and exhibit very high power-to-weight ratios — plus they don’t require a water-cooling system, oil or catalytic converter.”
Compact and powerful
Formed some eight years ago, Bladon Jets has relocated from its original base in Shropshire to larger premises in Coventry; and while the details behind the technology it is developing are being kept under wraps, what the company has essentially achieved is the re-design of the modern jet engine — as used in the world’s jumbo jets — and shrinking it to the size of two baked-bean cans placed end to end, making it suitable for installation in electric cars.
Perhaps the biggest challenge is producing the ‘miniature’ series of integrally bladed disks (or blisks) that compress the air as it flows axially through the turbo-shaft engine, which in turn is coupled to a high-speed generator that charges the batteries, making it the perfect on-board power source (or range extender) for an HEV.
“The blisks are not only small, they also have complex profiles and need watchmaker-type precision, if not better,” says Mr Lelliott. “We realised early on that conventional machining techniques such as milling were simply not possible due to access restrictions, so we looked at EDM and hit upon a winner — so much so that we now have a number of patents hinging on the use of EDM to produce these blades.”
Mr Lelliott says that not only was Sodick technology the best suited for the company’s needs, but the team from Coventry-based Sodi-Tech EDM Ltd (Tel: 024 7651 1677 – www.sodi-techedm.co.uk) was far more responsive than other suppliers.
“At the moment, we are essentially still a development company. Certain competitors of Sodi-Tech did not seem interested in supplying just one or two machines. Sodi-Tech, on the other hand, couldn’t wait to come aboard and help us realise the benefits of EDM technology. They know that Bladon Jets has real future potential and that many, many orders for future EDM machines could lie ahead.”
Machine mix

Bladon Jets has initially installed a re-conditioned Sodick AQ325L wire-cut EDM machine and a brand new Sodick AG35L solid-sink EDM machine — each configured differently to produce different parts of the turbine technology. The latter features a 32-station tool changer that allows the company to run round the clock producing development components. According to Sodick, the AG35L is the market’s fastest, high-precision solid-sink EDM; it also features linear-motor technology in the X, Y and Z axes, as well as Sodick Motion Control (SMC) for optimal spark gaps. Meanwhile, the AQ325L is a four-axis wire machine (each axis features linear-motor drives) with an automatic wire-threading capability.
Typically, each micro-jet engine has three or four different blade sizes — each with a different shape/profile, varying section, edge radii and taper from root to tip. Aircraft specification aluminium is the normal blade material at the front (cold) end of the engine, while Nimonic alloy is more typical at the hot end.
Bladon Jets is in discussions with a number of car manufacturers. Among the models to feature this technology is the Jaguar C-X75, a two-seater electric hybrid that uses twin micro-jet engines and can travel 900km on 60 litres of fuel. Moreover, it can accelerate from 0 to 62mph in just 3.5sec and has a top speed of 205mph. Currently, this car is a concept vehicle, but it demonstrates Jaguar’s ambitious vision for the future of electric-car travel.
Mr Lelliott says: “We have a technology and a product set to make big waves in automotive markets, and Sodick technology is the heartbeat of the manufacturing process. Improved performance and efficiency are achieved by closer tolerances and reduced hub-to-tip ratios.
“Additionally, reliability is improved further due to stress-free machining from solid material. Our patented manufacturing process enables the production of axial-flow turbines in smaller sizes than has previously been possible. Also, the process significantly reduces the development time and manufacturing cost for new engines.”
There are many other potential markets for the micro-jet engines produced by Bladon Jets, but it is the energy sector that harbours the next largest potential – a market that could be even bigger than automotive in time. “Using the engines for power generation as CHP (Combined Heat Power) units means they can be installed in domestic premises. Here, running on gas (or any liquid or gaseous fuel) they can generate electricity, while the waste heat can be used to warm the premises,” explains Mr Lelliott.