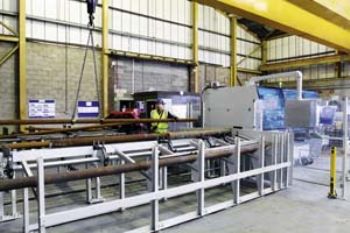
Lead time from receipt of order to dispatch has been cut from six days to just two days at the Oldham-based steel stockholder Taylorsteel (North West), following the installation in January of a new high-performance circular sawing machine — the first of its type in the UK.
Equipped with automatic cut-piece sorting, the Kasto Variospeed C15 CNC saw from Milton Keynes-based Kasto Ltd (www.kasto.uk.com) is typically 10-times faster at cutting than bandsaws used at the Taylorsteel site, two of which have since been redeployed elsewhere within the company’s holding group — Barrett Steel. Throughout the recession, Barrett’s engineering-steels division was profitable but accounted for only a small proportion of turnover, whereas orders placed on the group’s large construction-steel division declined. The company’s management decided to restructure the group by increasing the size of the engineering division.
This includes the Taylorsteel Oldham site, which specialises in carbon and alloy steels (both black and bright), a centre in Bradford that concentrates on supplying the gaskets market, and operations in Sheffield and Houston, Texas, which major on nickel alloys and other exotic materials. There are also engineering-division sites in Montrose, Ayr, Newcastle, Consett, Rotherham, Dudley and Bristol. The industries served include power generation, oil and gas, aerospace and automotive. In addition to sawing, ‘processing’ services include boring, chamfering, grinding and turning.
The business-growth initiative at Taylorsteel prompted close analysis of the types and sizes of materials being sawn, which are mainly round bar up to 530mm in diameter. Managing director Paul Carter established that 85% of the 1,200 cuts performed each day involved steel with diameters of 150mm or less and accounted for 50% of the tonnage throughput. “It was immediately apparent that half of our business could be made dramatically more efficient by investing in a circular saw. We identified the Kasto machine with multiple-order programming capability and automated cut-piece sorting as the best machine. Irrespective of whether we are cutting softer steels like EN8 or harder, alloyed steels such as EN19 and EN24, the Variospeed is 10-times faster than our bandsaws.”
While bundle cutting 20 bars at a time on a bandsaw reduces time per cut, theoretically to the same time as on the circular saw, Taylor-steel’s experience is that when clamping so many bars, one or more of them invariably spins during cutting and breaks a bi-metal blade. This could happen two or three times during a batch, slowing production and adding considerably to ‘tooling’ costs.
Enhanced image

Since the circular saw was installed, customer perception of the stockholder’s service has been enhanced. Apart from receiving material a lot faster, customers notice that the quality of the cut faces is much better than when it was ‘bandsawn’. Indeed, it is now so smooth that frequently bar does not have to be faced prior to machining.
Another benefit is that, when a batch of billets or bars has been sawn and sorted, there is less swarf on the parts in the bins, avoiding Taylorsteel having to clean it off by hand before delivery to the customer. As a circular saw blade takes a chip, rather like a milling cutter, instead of generating the fine swarf that is typical of bandsawing, it is easier to separate from parts as they are being cut on the Variospeed. Similarly, any chips that find their way into the parts bins can be removed quickly.
Moreover, flood coolant used in bandsawing tends to cause swarf to stick to the cut pieces, whereas spray mist coolant used in the Vario-speed circular saw prevents this from happening. There is never any coolant on the floor around the machine; and from a cost perspective, Mr Carter estimates that there has been a 100-fold decrease in the amount of coolant consumed by the circular saw, compared with a typical bandsaw.
For cutting mild steels, the stockholder has standardised on 2mm-thick cermet-tipped circular saw blades from Kanefusa, while PVD-coated varieties are used when processing tougher alloy steels. Blades 460mm in diameter cut stock with diameters from 150mm down to 60mm. As the stock becomes smaller, the blade speed is slowed to keep chip load per tooth correct. This avoids having to change the blade too frequently and allows long periods of uninterrupted production. Blades 360mm in diameter are used for cutting smaller-diameter stock.
Automated operation

Taylorsteel has opted for a 10-position chain-type in-feed magazine, separated by divider pins and with each position holding stock up to 6m long for processing. At the end of the day shift, 10 sequential programs detailing material type and diameter, saw blade, and number and length of the cut pieces required are entered into the TechnoControl CNC system. This uses proprietary Kasto software running on Siemens hardware, and it contains built-in knowledge of the optimum speeds and feeds for cutting a wide range of materials with different types of blade. Moreover, the database can be customised and extended by the user.
A pulling vice with a stroke of 2m automatically feeds each length of material successively through the saw, so orders are completed with minimal operator attendance during the day. Batch size ranges from 10 parts to several thousand.
After lights-out running, staff arrive next morning to find batches of accurate, swarf-free parts ready for immediate transfer by crane to the dispatch area. They have already been sorted into bins, as the control system instructs the material table to pivot horizontally into one of six pre-determined locations, according to the type of cut piece. There are five bins for cut pieces and one for trim cuts — three positioned each ‘side’ of the machine. The three bins at the back ‘side’ can be replaced with a movable table that can accept longer bar lengths — up to 2m. Rest pieces are returned to an inclined magazine at the front of the in-feed table.
That’s handy
Mr Carter highlights a useful feature of the control that helps when cutting more than one order from a single type and size of bar. The control runs the order for the longer parts first, constantly monitoring the remaining length of bar. When it becomes too short to cut another long part, the control automatically swaps to cutting the shorter length, if that is possible. When a new bar is loaded, it reverts to processing the longer length and continues swapping between jobs until the order for the longer parts is complete, whereupon the batch of shorter lengths is finished. Overall, the time to complete both jobs is less, and rest-piece lengths are shorter.
In conclusion, Mr Carter says: “The Kasto circular saw is transforming our business, allowing us to compete more effectively on price and deliver a better-quality product. As a result, we are winning a lot of new business. It is also good for morale when staff see the company invest in top-class plant like the Variospeed. The next step will be to look at rationalising storage of our material, which is currently in conventional racking. We took the precaution of specifying a Kasto saw control that can interface with an automated storage and retrieval system, which we see as part of the future for our company.”