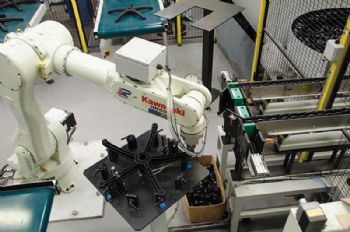
Wigan-based Suscom Industries, which supplies components to the office furniture industry, stopped all in-house production over 20 years ago and elected to ‘offshore’ the work.
Today, after investing £750,000, it is producing office-chair bases to a higher quality level, more profitably and with greater control over stock and availability.
The investment has seen the return of injection moulding, in the form of two 600-tonne Romi presses, with all the handling — plus assembly of the castors — managed by three Kawasaki robots (
www.kawasakirobot.co.uk).
Production manager Joel Rockwood believes that developing a new chair base with automation in mind has given Suscom a far better product than the currently available generic designs.
“Unlike generic imports, mouldings that come straight from our new tooling require no further coatings or fillers, have no surface imperfections and are a much stronger product overall.
“The cell is absolutely consistent and reliable in its output of 1,000 chair bases per 12hr shift, which we manage with just two operators. The robot system has surpassed what was expected of it — both in speed and in maintaining a very clean and orderly environment.”
The system has also had a significant impact on Suscom’s customer service. “We could see prices rising in China, so creating our own in-house design made sense.
“The payoff for customers is clear, as we have maintained — and even lowered — our prices, together with adding value by assembling castors and delivering an all-round better product.”