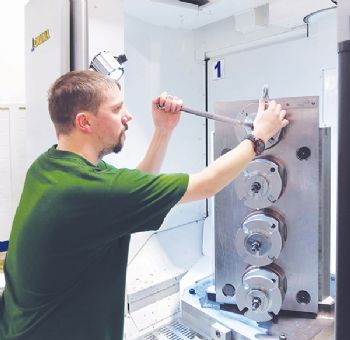
Ted Fort, a former Rolls-Royce engineer and chairman of Fort Vale Engineering, recently become an octogenarian. He started buying Okuma machining centres and lathes more than 40 years ago for his company, which is now a global market leader for the manufacture of stainless-steel valves and ancillaries used in the tank container industry for the transportation of bulk liquids and gases by road, rail and sea.
Andrew Bryce, the company’s ‘innovation director’, who joined as a machinist in the late 1980s, continues to buy Japanese-built Okuma machines from UK agent Thames Ditton-based NCMT Ltd (
www.ncmt.co.uk).
Eight of the 40 CNC machine tools in the Burnley factory are currently from that source, the most recent purchase (in November 2016) being an MA600 horizontal machining centre with the ability to turn-cut — Okuma’s terminology for interpolation turning.
This entails circular movement of the machine’s X and Y axes, coupled with synchronous rotation of a turning tool in the spindle and forward feed in Z, to undertake internal boring or external turning that can include complex features.
Mr Bryce said: “As Okuma produces its own CNC system, as well as the spindle, drives, rotary encoders and scales, the control’s functionality is matched to the machine, allowing perfect synchronisation during the turn-cut process.
“When we started to evaluate our next HMC purchase, the Okuma solution with turn-cut from NCMT was the obvious choice, because other machine platforms offering interpolation turning could not match its performance.”
Cost savings
Process improvement engineer Stephen Maher said: “Interpolation turning is an extremely useful addition. Previously, when producing a newly designed component with a stepped cross-bore containing radii, counter-bores and chamfers, we had to specify and purchase up to six special form cutters to generate that single profile; these tools would typically take up to six weeks to arrive.
“Now, with turn-cut, we can produce the part immediately. One roughing and one finishing boring bar with indexable inserts does the same work, saving on costly cutters as well as shortening programming and cycle times. The process also significantly compresses the lead time from concept to finished component.”
Production co-ordinator Carl Tillotson highlighted the ergonomic position of the control on the latest machine; he no longer has to look over his shoulder when proving out jobs. He made reference to the OSP-P300MA control system’s extra features, such as allowing the operator to customise the touch-screen layout to show different page functions at the same time.
Comparing the performance of an earlier Okuma MA500 HMC and its OSP200 control with the latest MA600, Mr Tillotson says that every job transferred from the older machine has shown a cycle time improvement of around one third, using the identical program. For example, six parts on a tombstone can be completed in 20 rather than 30min.
Moreover, the new machine’s rigidity is such that all tooling now runs at the manufacturer’s recommended speeds and feed rates; and the 70-bar coolant system means that the service life of each cutter is longer and more predictable, even though 316 and 304 stainless steels are being machined nearly all the time.
Mr Tillotson also says that swarf ejection is particularly efficient.
“The accuracy of profiled bore details produced by finish turn-cutting is much better than when using form tools — and there are no sharp transitions between features. Tolerances down to 10µm are held, and surface finishes as high
as 0.4Ra are achieved; this is crucial to ensuring that there are no leak paths in the valves.”
Due to the success of the turn-cut feature, the production team at Fort Vale Engineering is now looking at extending its use to threading and eccentric boring to replace turning and milling. The machining of scrolls on valve
sealing faces instead of turning them can also be undertaken.
In conclusion, Mr Bryce said: “The technique is helping us to innovate and stay ahead of our competitors through shorter lead times in programming, tooling acquisition and cycle times.
“It is therefore allowing us to achieve one of our prime objectives — namely, faster deliveries to customers.”