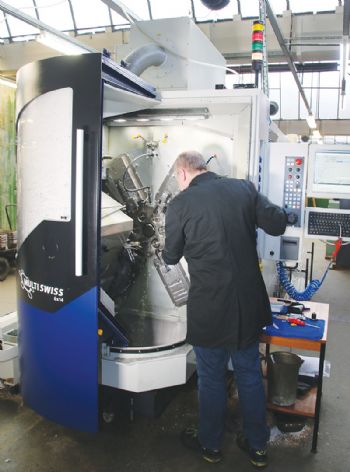
Almost 78 years after Tenable Screw was founded by a Swiss watchmaker as a manufacturer of screws, the company has become one of the UK’s largest sub-contract manufacturers of turned parts.
It has three manufacturing sites — in Marlborough, Coventry and its headquarters in Wimbledon, South London — and more than 250 machine tools.
These include 71 coil-fed Escomatics, 26 multi-spindle machines, 56 sliding-head turning centres and four fixed-head turning centres.
Together, they produce millions of components every month, ranging from connector pins and sockets to bolts, screws and much more for the electronics, instrumentation and control, automotive, aerospace, medical, defence, transport and telecommunications sectors.
Quantities range from prototypes to batches of more than 100,000 parts.
Tenable Screw has a live customer base of over 250 companies and invests 10% of its annual turnover in new technology, with one of its latest investments being a Tornos MultiSwiss 6X14 from Coalville-based Tornos UK Ltd (
www.tornos.com).
Tenable Screw commercial director Nigel Schlaefli said: “While we initially used the MultiSwiss as a flexible production centre to support our single-spindle machines, it is now dedicated to producing one family of components.”
Just a few months after installing the MultiSwiss, Tenable Screw won a long-term automotive contract for a family of stainless-steel pins requiring numerous external turning operations, as well as knurling, drilling and parting-off. The contract is for 1,500,000 parts a year.
The company trialled the automotive part on one of its sliding-head turning centres and achieved an output of 1.5 parts per min; the MultiSwiss was capable of producing nine parts per min.
Mr Schlaefli said: “To meet the demands of this specific contract, we would have had to commit staff to running six sliding-head machines round the clock.
"The MultiSwiss achieves the same output by running for just 17-18hr a day.
"We can run the machine during a day shift, change tools and re-stock the bar feeder at the end of the shift and then run for an extra 8-9hr unmanned.”
Consistent quality
Paul Kelley, the manager responsible for more than 60 CNC machine tools at Tenable Screw, said: “If we were producing this automotive part on five or six machines, there would inevitably be a variation in CPK values between the machines.
“While the part has an average tolerance band of ±20µm, the MultiSwiss easily maintains a band of less than ±10µm, which improves our CPK and SPC values considerably.
“Furthermore, because each spindle on the MultiSwiss works independently — unlike conventional multi-spindle or CAM-auto machines — we can optimise the speed of each spindle for specific operations.
“This capability considerably improves surface finishes and contributes to improved tool life, compared to other production machines.”
Also contributing to both quality and good tool life is the hydrostatic spindle technology used by the Tornos MultiSwiss.
Mr Kelley said: “Over an extended period of time, roller bearings in spindle assemblies suffer wear, adversely affecting component quality.
"The hydrostatic spindle technology on the Tornos eliminates wear; it also eliminates vibration in the spindle head, enhancing both component quality and surface finish.
“Furthermore, the MultiSwiss will run for two days without needing a tool change — and even then, we are only changing inserts as a precautionary measure.
“The only tool we change on a daily basis is the one for knurling. To put this in context, we are producing 18,000 stainless steel parts before we change inserts, which is at least double the tool-life of the single-spindle machines.”
The MultiSwiss at Tenable Screw has a Fanuc CNC, which Mr Kelley says is particularly easy to use. “The MultiSwiss has 14 linear axes, seven C axes and up to 18 toolstations.
"Despite the number of axes and tool positions, the machine is significantly easier to program than a single-spindle sliding-head machine.
“We apply G-code programming and determine the number of operations for each spindle. Combining these features with a well-lit and easy-to-access work envelope, the MultiSwiss is both fast and easy to set up.
"This ease of programming is certainly beneficial, as there is a distinct lack of skilled CNC machine operators and programmers in the UK.
"The MultiSwiss effectively reduces the number of highly skilled staff we need for a given productivity.”