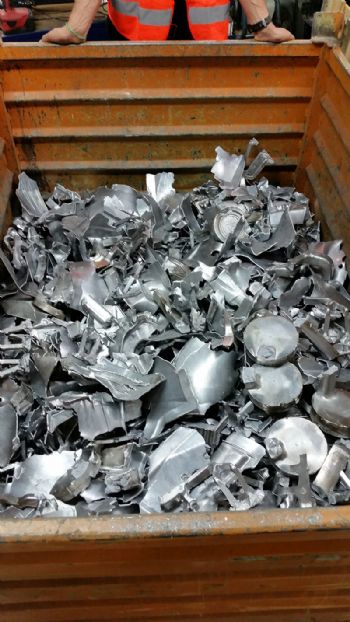
Every year, BMW Group’s light-alloy foundry at Landshut produces around 5 million aluminium castings (with a total weight of 84,000 tonnes) — such as engine components or structural components for vehicle bodies — using five different casting processes.
In the past, scrap items, which can be up to 2,000 x 1,400mm, were collected in containers (without being shredded), removed from the basement of the foundry and returned to the melting process.
However, because these cast aluminium parts took up a lot of space, the collection containers had to be emptied frequently.
When BMW came to renew the casting cells it had an opportunity to review its scrap-handling procedures; it asked Erdwich Zerkleinerungs-Systeme GmbH (EZS) (
www.erdwich.com) to design a system to collect and shred the foundry’s aluminium waste directly from the presses.
EZS designed a machine based on its RM 1350 pre-shredder; to date, seven systems with soundproof enclosures have been installed for the eight casting cells and punch presses in the BMW plant.
EZS project manager Richard Adelwarth said: “Parts that are to be returned to the melting process now fall from the pressing plant directly into the hopper of the pre-shredder and then into a container measuring 1,400 x 1,400 x 900mm.
"When the container is full, it is transported outside and emptied into a larger container that is subsequently taken to the smelter.
"The shredding process has reduced the volume of cast parts by 50-60%.”
As soon as all the casting cells have been replaced, a conveyor system will be installed. This will take shredded rejects directly into the large container, eliminating the need for the smaller containers.