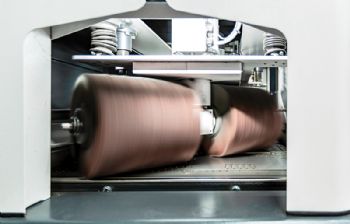
The combination of improved laser processing and increased customer demand led to a bottleneck at AA Sheet Metal, when it came to deburring and surface graining.
Traditionally, these were manual operations at the Norwich-based sub-contract sheet metal company, but increasing volumes of work necessitated an automated solution.
AA Sheet Metal was formed in 1987 by co-directors Alan Lappin and Alan Smith to serve the food-packaging industry and commercial catering-equipment sectors.
The work undertaken involved laser cutting flat stainless-steel sheet, then forming and welding it to produce fabrications in relatively small batch quantities.
With year-on-year growth came the need to continually invest (and relocate three times), leading eventually to the recent installation of a flat-bed fibre laser to replace a CO2 laser machine.
Mr Lappin said: “Everything we produce goes through our laser machine, and the move to fibre gave our productivity a massive boost.
“It also meant we had more parts that required edge finishing; and as this was done manually, the extra production put greater pressure on the team.
“This got us thinking about reducing the manual content of our deburring to improve work-flow — and address health-and-safety considerations such as ‘white finger’ resulting from the use of manual air tools.”

When a long-standing customer doubled its volume of work, AA Sheet Metal’s need to automate deburring was somewhat forced on it, resulting in the installation of a Timesavers Series 32 deburring and surface-finishing machine from Christchurch-based Ellesco Ltd (
www.ellesco.co.uk).
A particular requirement of the food industry is that all processing equipment has to be kept spotlessly clean by frequent and intensive cleaning.
Moreover, the nature of this equipment requires a lot of manual intervention, reaching into dark corners through slots and along edges.
Therefore, rounded edges are required to eliminate any risks to the operator from sharp corners; also needed is the type of finish that can be readily cleaned with a pressure washer.
Multi-tasking
The Timesavers Series 32 machine (a 32-1100-WRB) at AA Sheet Metal can undertake automatic deburring, finishing, edge rounding and the removal of laser oxide skin.
This capability is provided by a combination of a wide abrasive belt and four rotary brushes; and thanks to the use of a vacuum table, parts as small as 50mm square can be processed without any manual input.
A Siemens HMI located on the front corner of the machine allows the operator to quickly set all of the processing parameters, including grind height (between 0 and 100mm) and table speed (0.2 to 8m/min).

Series 32 machines can undertake burr removal from the edges of laser-cut parts (including those that are plastic-coated, without disturbing the plastic), as well as those that have been cut by water jet, punched or guillotined.
These machines can also process a wide range of materials, including various steels, stainless steels, aluminium, copper and other metals.
For the type of work produced by AA Sheet Metal, visual appearance is important, so being able to produce consistent brushed finishes and corner radii is a major benefit.
Additionally, the speed at which parts can be processed by the Timesavers machine means that both sides of a part can be treated equally, with the finish on a completed cabinet as good on the inside as on the outside.
AA Sheet Metal foreman Simon Miller said: “We can now process batches irrespective of size and know that every part will look identical.
“Furthermore, it makes no difference how complex the part shape is, as we know that every edge will be deburred/rounded to the same degree; and the fact that we can deburr plastic-coated material without damaging the metal surface is a major advantage.”
The technology behind this edge consistency is Timesavers’ Rotary Carousel Brush system, which hits every edge “from every-which-way”, thereby ensuring that an equal edge break is achieved; previous twin-brush systems only worked with the flow of material or across it at 90deg.
Improved productivity
In addition to the consistency and quality generated by the Timesavers 32-1100-WRB, the improved productivity was also vital, as the business is continuing to grow.
Mr Lappin said: “The Timesavers machine is the equivalent of having 10 people manually deburring, so these people are now free to use their skills more productively — fabricating and welding.

“Deburring by hand is extremely time-consuming and poses health issues; with the Timesavers machine having dust extraction, the workplace is now dust-free, and operators no longer have any concerns over the potential damage that using hand tools can bring.”
The Timesavers machine was recommended to AA Sheet Metal by one of its customers using a similar machine from Ellesco; other points in its favour were its versatility, fast set-up and ease of use — irrespective of batch size.
What Mr Lappin describes as ‘intense’ training was provided to Mr Miller (and two others) while the machine was being commissioned; he was then able to train others to set and operate the machine in just 15min.
Mr Lappin said: “That short time was all that was needed, as the machine really is that straightforward to operate — and we know that the support is there at the end of the phone at Ellesco, if we ever have any questions.
“Having the machine has allowed us to look for larger-volume work, knowing that we no longer have that bottleneck when it comes to deburring and graining.”