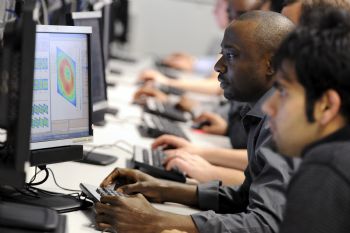
With the growing popularity of advanced composite materials in all industry sectors, especially automotive and aerospace engineering, universities are keen to understand how to develop students’ knowledge to help plug
a skills gap.
David Hughes, senior lecturer in materials engineering at Teesside University, is addressing the problem through research and instruction in composites engineering.
In the UK, there are currently many people working on composite materials in the broadest sense and many working on manufacturing methods, but the largest skills gap is
for people who can design in composites.
In partnership with Siemens PLM Software, Teesside University uses the Fibersim suite of software for composites engineering in its teaching and research.
It has embedded this software in its engineering courses and is the only university in the UK to use Fibersim in its degree programmes; students can learn how to create a digital twin of a composite part that links analysis, design and manufacturing — everything needed for composites engineering.
Teesside University also uses Siemens’ NX software for product development and NX Nastran software for structural simulation, as part of a comprehensive instruction programme that includes practical hands-on projects and facilities.
The goal is to create students who understand digital tools, the way engineering is going and how markets are developing.
More and more is done in a simulation environment, rather than in more traditional development processes to support this approach.
Dr Hughes’ course in composites is mandatory in the aerospace degree programme, and 40-60 students are enrolled in the class each semester.
He said: “A core learning outcome in the aerospace degree is knowledge of aerospace materials, which include high-temperature alloys and composite materials. It’s a core topic.”