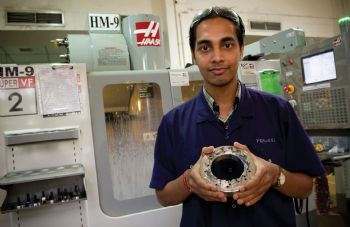
In the early 1990s, the American precision engineering firm Turbocam Inc was being urged by a customer in India to take advantage of new, more-relaxed foreign direct investment legislation and open a factory in the country.
The reasoning was that the Indian company would then have access to the high-quality parts it needed but would no longer have to pay for them with foreign currency. In exchange, Turbocam could gain a foothold in one of the world’s fastest-growing economies. It was a long-term investment with a degree of risk, but the customer assured Turbocam that he would keep the new factory busy.
Subsidiaries are usually set up in the image of the parent company. Turbocam Inc is a successful and highly respected organisation, serving some of the biggest and best-known names in the aerospace, automotive, industrial and marine sectors with bladed production parts for turbo machinery. When it established Turbocam India Pvt, the factory was equipped with a brand of CNC machine tools that the group’s senior managers knew and trusted.
Savio Carvalho, a director of Goa-based Turbocam India Pvt Ltd, said: “Back in the early days, we were very much guided by the head office in the USA. This included our choice of capital equipment. However, I think a turning point came in 2001, when we got a large order through Turbocam Europe for five-axis insulator segments for the Large Hadron Collider, in Switzerland. We eventually made about 60,000 parts, after which I think we ‘grew up’ in the eyes of our American principal. They saw that we could do a lot here.”
New CNC machine
The order from CERN (the European Organisation for Nuclear Research) was worth over $1 million. Once the final parts were delivered, the Indian subsidiary had the resources it needed to buy better and newer CNC machines. “We were already in contact with the local Haas distributor, who told us about a local company using a Haas machine – a VF-3,” said Mr Carvalho. “We went along and had a look at it; we also asked the owner his opinion of the machine, and he was very enthusiastic.”

In 2004, the company bought a Haas VF-2SS
(www.haascnc.com) — the first of what would eventually turn out to be many Haas CNC machine tools at Turbocam India. However, Mr Carvalho recalls that it was hardly used for the first year. “Most of the work we were doing at the time was five-axis. We didn’t really have any work for the four-axis Haas, but we took the opportunity to learn how to get the most out of the machine, so we used the time well.”
However, Turbocam India was soon using the Haas machine to rough-cut the turbine blades, before finishing them on its five-axis machines. “We used the Haas to rough in two set-ups; as a result, our roughing times decreased substantially. We knew that the Haas machine was fast and reliable, but we really needed to start using it to finish-machine the blades.”
By coincidence, some of the orders the company received at that time were for less-complex turbine blades that could be machined using just four axes. From this point onwards, the Haas was a fully fledged production machine. “In 2005, we cut some test parts for Cummins,” says Mr Carvalho. “A little later, they gave us ‘the green light’, saying that they were planning to go into production in a year, and wanted us to produce 10,000 parts per month. We needed to get some more machines quickly, but not everyone voted to go with the Haas machines at that time.”
Factory visit
By early 2006, the company still had not decided what machine tools to buy. Turbocam India was convinced that it should invest in Haas machines, but the head office in the USA had slightly different ideas. To build his case, Mr Carvalho travelled with Onno Weststrat (of Turbocam Netherlands) to Hannover to visit the Haas Automation Europe stand at EMO, the biennial European manufacturing show. From there, they flew on to Turbocam’s US headquarters in New Hampshire, where Mr Carvalho met with his colleagues and presented his argument in favour of Haas machines.

They were not entirely convinced. “I told Terrence Miranda, managing director of Haas India, that he had to convince the Americans to buy the Haas machines. He arranged with Haas Inc to fly Elliot Wilkins — our technical director — and Keith Bainbridge — our main machinist — to the Haas factory in Oxnard, California. They were really impressed with how the factory was set up. They saw how Haas builds its machines — and the number of Haas machines the company uses on its own production line. We re-submitted our proposal to the head office, and they gave us the go-ahead for eight Haas machines — two lathes and six mills.”
A few years later, Turbocam was running 16 Haas mills and four lathes — and making up to 14,000 of the Cummins turbine parts every month. “Originally, we turned this part from bar, but it wasn’t particularly cost-effective and created a lot of waste.Now, our customer manufactures the forgings and sends us the components once they have been rough-turned; we do the finish-turning and milling. Finally, one part in 11 is checked 100% in our air-conditioned CMM room.”
At the last count, Turbocam India had 23 Haas machining centres and five Haas lathes. In a typical week, the machines are switched on at 6.30am on Monday and switched off at 10.30pm on Saturday. Sundays are set aside for preventive maintenance.