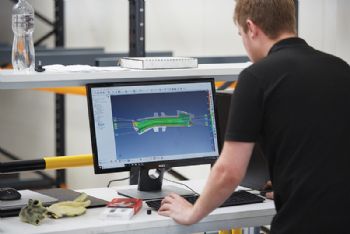
Coventry-based Impression Technologies, a specialist in aluminium lightweighting, has released a new white paper introducing the benefits of its new ‘hot form quench’ (HFQ) process, which has been developed to offer a “step-change in aluminium forming” across a range of industries, including automotive and aerospace.
The white paper — ‘Hot Form Quench (HFQ) Technology: The new international standard for cost-effective automotive lightweighting using aluminium’ — outlines how manufacturers can easily and cost-effectively replace steel or thin-gauge aluminium components using HFQ.
It describes the benefits and the process of HFQ in detail, along with examples and case studies that illustrate how it can be applied and what can be achieved.
Jonathan Watkins, CEO of Impression Technologies, said (
www.impression-technologies.com): “The automotive industry is on a constant mission to improve structural strength, integrity, consistency, durability and safety, all while reducing weight and cost.
“HFQ is a patented process that enables the low-cost production of high-strength aluminium parts.
“The benefits of aluminium in automotive applications are widely known, but there have been concerns around cost, strength and production rate.
“HFQ addresses these with a high cycle rate and the ability to form deep-drawn and complex shapes from high-strength and ultra-high-strength aluminium.
“It is an ideal process for reducing mass and improving efficiency across all automotive applications, from body in white (BIW) and chassis to electric vehicle battery enclosures.
“The process also removes the need for reinforcing panels, while improved dimensional control eliminates the need for springback compensation in tool and part design, simplifying downstream assembly operations.
“HFQ combines heat treatment and pressing; the process is also easy to adopt as it can use existing press and tooling technologies with a single-draw operation.”