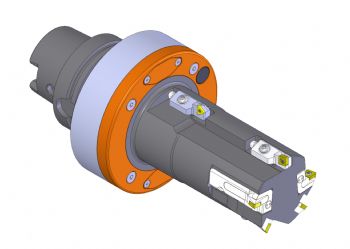
When approached by a global automotive manufacturer (based in India) to assist with improving process and cycle times
on its engine cylinder bore machining, Cornwall-based Rigibore (
www.rigibore.com) made full use of its expertise in the design and manufacture of specialist boring tools.
Using its own design software coupled with its closed-loop tool compensation system, Rigibore was able to reduce machining time on the cast-iron cylinder blocks.
One of the challenges faced by the company was the common occurrence of size drift on the finished bores — caused by material inconsistencies, temperature variations and insert wear.
Rigibore’s Zenith is a completely automated boring system, adjusting the ActiveEdge boring bars’ cutting edges to achieve near-instantaneous precision tolerances without operator intervention.
The process transfers the measured value obtained by gauging or probing cycles to the machine tool control, triggering tool compensation to an accuracy of 1µm to return the next machined bore to nominal tolerance.
The system not only calculates the value of the adjustment required but also provides confirmation that it has been completed and that the new compensation value has been achieved.
To streamline the machining process, Rigibore used its RADS design software to create a custom boring tool for this project that would semi-finish to a diameter of 75.68mm, then finish-bore to 75.934mm; a chamfering insert cartridge was added to break the edge at the mouth of the bore.
The resulting design featured three semi-finishing cartridges and two ActiveEdge cartridges for the finishing cut.
These were positioned in such a way that when the cut is complete, the tool can be offset to provide clearance for a rapid retraction without leaving any withdrawal marks.
This feature saved around 15sec per bore or 1min per cylinder block.