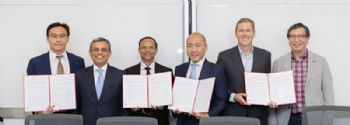
Singapore-based research, product development and commercialisation company Bralco Advanced Materials Pte Ltd has signed a Memorandum of Understanding (MoU) with GE Additive for the development of 3-D printed magnetic components — as used in the aerospace, medical, automotive, energy, industrial automation and robotics industries.
The MoU aims to “progress the 3-D printing of magnetic components in the Asia Pacific region”.
The companies say that Bralco’s strength in magnetic materials, combined with GE Additive’s expertise in powder manufacturing and additive-machine technology, will enable Bralco to “accelerate the development of soft and hard magnets and components that have complex shapes, differentiated magnetic fields and high mechanical strength, while being capable of operating at elevated temperatures, high frequencies and high torque conditions — as necessary for demanding applications such as the drive motors of electric vehicles”.
The MoU contemplates Bralco being given access to GE Additive’s AddWorks engineering consultancy team and its AP&C materials division, thereby enabling it to shorten the product development and commercialisation cycle.
The MoU also contemplates the potential in the future for the appointment of Bralco as a service provider in the Asia Pacific region to print parts and components, using GE Additive machines and powders based on Bralco’s magnetic materials compositions.
Amit Nanavati, Bralco’s founder and CEO (
www.bralcoadvancedmaterials.com), said: “This collaboration is a major milestone for us, coming at a time when the demand for soft and hard magnets is growing rapidly due to their use in every aspect of modern life — be it health care, mobility, personal communication devices, renewable energy or robotics.
"Moreover, the adoption of additive manufacturing technology will save millions of dollars in material cost, due to the additive nature of this technology compared to traditional manufacturing processes.”