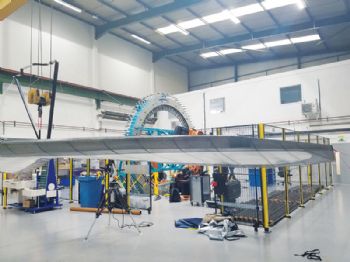
Hang glider design could take its first significant step forward in two decades, thanks to a collaboration between the UK’s only manufacturer of these ‘aircraft ’and the University of Sheffield’s Advanced Manufacturing Research Centre (AMRC).
Peak District-based Avian Hang Gliders (
www.avianonline.co.uk) approached the AMRC for help in developing a precise 3-D model of the wing, which could then be fed back into analysis to lead to a ‘more aerodynamically optimised design’ (the AMRC is part of the High Value Manufacturing Catapult).
Avian Hang Gliders director Tim Swait said: “In the early 2000s hang gliders became ‘topless’; they lost the king post, the top rigging went and the stability systems were all integrated into the wing. Since then, there has been incremental developments but there has not been any real step changes.
Avian is trying to identify where we can make significant difference in hang glider design, as we know their efficiency can be quite a bit higher than it is at the moment.
Having an accurate 3-D representation of what the glider truly is will be the first step forward.”
A glider, supplied by Avian, was scanned in the AMRC’s Composite Centre using a Hexagon Romer arm and analysed using Verisurf software. The scan was carried out with the glider hanging upside down to make the aircraft more representative of being flown.
In flight, airflow over the wing creates pressure differences which produce lift, but also changes the shape of the fabric sail. This could not be replicated when scanning, so AMRC engineers used the force of gravity to ‘create tension in the glider’, which acted as an ‘appropriate approximation’.
AMRC development engineer James Grigalis said: “When you pull the sail tight, all the struts inside the wing bend and tension up; it is very hard to get a CAD model of that without doing something like a scan.
“We could have hung weights off the wings to create the tension, but then you’re not tensioning the sails in the right way.”
Dr Swait added: “What we are trying to do is get the shape that the glider has in the air because that is different to what it is on the ground.
“Hang gliders are fundamentally flexible; you have flexible fabric, a sail and a carbon fibre frame that isn’t rigid over that scale.
“Sections can be metres long and fairly thin, so there is quite a significant curvature in everything.
“Now we have the scan data, we can feed the computer model with the current shape of the glider and use the model to optimise what shape it should be.
“Then we can work back from that ideal shape to what we make, and thereby get the glider back to being that ideal shape when it is in the air.”