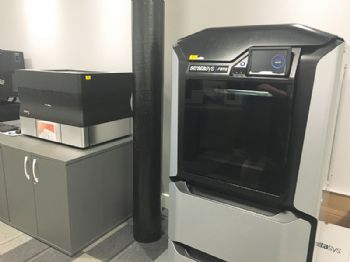
A 120-year-old former cotton mill in suburban Oldham might not be the sort of location you would immediately associate with Japanese production philosophies, but it is home to Crane Payment Innovations (CPI), which in 2010 acquired Oldham-based Money Controls.
Founded 43 years earlier, the latter’s automated coin-handling systems were originally used on fruit machines; it later expanded into applications such as vending machines and self-service checkouts.
Today, CPI is a global concern that produces an extensive range of payment-handling technologies, from cashless products, note and coin validators and recyclers to coin hoppers and dispensers.
It counts UK supermarket giants Tesco and ASDA among its customers.
At CPI’s appropriately named Coin House site in Royton, Kaizen (the Japanese word for ‘improvement’) is its ‘guiding light’.
The idea is that small positive changes can produce major improvements that will reduce defects, eliminate waste, boost productivity, encourage ‘worker purpose’ and promote innovation; this is also an approach that helped CPI to identify 3-D printing as a ‘transformational’ technology.
Dave Taylor, a principal mechanical design engineer with 16 years of experience in the payment-handling sector, said: “Customers always want an evolution in product performance, and that is where 3-D printing comes in.
“For us to justify getting a 3-D printer, we had to prove what it was going to save us and what the benefits were.
“We saw an opportunity to save time and cost in the development process. It is quite clear that parts will be cheaper and faster to produce, and as long as they are functional — which they are — it is a ‘no-brainer’.”
Development tool
To help with the development and production of its coin-recognising, sorting and dispensing systems, CPI’s first foray into 3-D printing came in the form of a Stratasys Objet30 Pro.
Supplied by Derbyshire-based SYS Systems (a Stratasys UK platinum partner), this desk-top machine uses PolyJet technology (based on traditional ink-jet printing).
Its success resulted in CPI adding to its capabilities with a Stratasys F370; this uses the fused deposition modelling (FDM) technique of building detailed models layer by layer in ultra-tough materials — from the bottom up.
Mr Taylor said: “Once we’d used the Objet30 Pro for a few years, we started to see the potential benefits of printing our jigs and fixtures, which is why we looked at FDM technology.
“We chose the F370 because of the large bed size, and it gives us incredible time and cost savings.

“Now we have the best of both worlds: accuracy and a smooth surface finish with the Objet, plus speed and toughness with the F370, which has been incredibly reliable.
“Indeed, we’ve not had a single failed print in a year and it’s done 4,000hr of work.
“Initially, 3-D printing for us was all about functional prototyping and speed of iteration, but its application has evolved; now, 80% of its output is for jigs, fixtures and production support equipment.
“Previously, these parts would be made from wood, aluminium or plastic at a company that would charge us hundreds or thousands of pounds for them, and they weren’t repeatable.
“3-D printing has completely changed all this; we can have new parts available the next day, and the price advantage is incredible.
“Moreover, we have had virtually no complaints about the parts we print, which are used hundreds of times a day — and the materials we use cope well with the punishment they get.
“With regard to prototypes, we used to buy these in at 10-times the cost of 3-D printing them.
“Using even the fastest methods when out-sourcing, it would take a week to get a model back.
“If you are making prototypes for a live project, you have to iterate quickly to meet the expectations of the business and customer.
“With 3-D printing, a part can be ready the next morning, so we’ve been able to shift most of our prototyping in house.”
CPI has 3-D printing down to ‘such a fine art’ that it makes bespoke manufacturing aids that take into consideration the needs of individual assemblers and operators, incorporating features that help to limit the risk of conditions such as repetitive strain injury.
In conclusion, Mr Taylor said: “If our 3-D printers were taken away now it would be like having a vital part of our business missing.
“We often solve a problem by printing a part; the process is becoming as accepted as using a laser ink printer.”