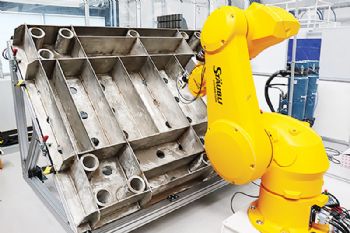
Rotherham-based Nuclear AMRC engineers have successfully demonstrated automated grinding techniques for nuclear components, as part of a European collaboration to develop intelligent robot technologies.
The centre’s robotic and metrology engineers have developed automated techniques for grinding out welds on a nuclear fuel rack base, and for deburring tube structures, using a variety of methods.
The research has been carried out as part of the 6 million euro Coroma project, which ran from 2016 to 2019 and
was funded through the European Horizon 2020 programme.
The three-year project has brought together companies and research institutions from around Europe to develop cognitively enhanced modular industrial robots that can perform a range of manufacturing tasks with minimal input from human operators.
The applications developed by the Nuclear AMRC team were identified by one of the industrial partners — Spanish nuclear manufacturer Ensa — as a test of the Coroma technologies in a real workshop environment.
Weld grinding of the fuel rack base is currently done manually and takes around 80hr, with prolonged use of hand-held grinders putting operators’ health at risk from harmful vibrations.
The Nuclear AMRC team developed a full-scale technology demonstrator, integrating a variety of innovative digital manufacturing technologies developed by the other Coroma partners integrated with a large Staübli robotic arm.
These technologies include visual scanning and analysis to map where grinding is required — a challenging task when the actual fabrication does not precisely match the CAD model.
The Coroma partners developed a novel scanning technology that could also be deployed for processes such as welding and additive manufacturing.
Other innovations include optimisation software to determine the most efficient way to remove the excess material, and location monitoring techniques to ensure that the robot remains accurately positioned relative to the workpiece.
All of these physical and digital technologies had to be integrated into a single system.
Nuclear AMRC research engineer Ozan Gurda (
www.namrc.co.uk) said: “You have lots of different hardware and software trying to talk to each other. What we wanted to develop was a versatile system, so that you can do the integration with one click.”
The team were also challenged to deliver a cost-effective solution that will make economic sense for smaller businesses.
“What is making it cost-effective is the engineering effort we put in.
“It is important that it is robot-independent, so if you take the end effector out and put it on another robot, it’s a one-click integration. That gives you the ability to use it in different environments.”
Compared with conventional robot programming, the Coroma approach demonstrated time savings of more than 70% for each pocket in the rack base — saving more than 40hr for the complete assembly.