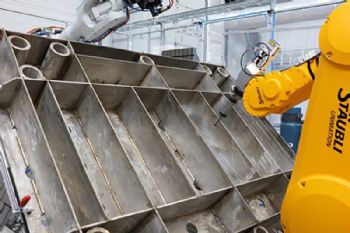
A 2-D laser profile sensor from Micro-Epsilon (
www.micro-epsilon.co.uk) is being used by the Nuclear Advanced Manufacturing and Research Centre (Nuclear AMRC) in Rotherham on a project to develop a smart robotic grinding/deburring solution for welded components.
The sensor is mounted to a robot end effector (the device at the end of a robotic arm, designed to interact with the environment) and measures the profile of welded joints and planar surfaces.
Coroma is a robotic system development and integration project to automate a variety of secondary finishing operations including grinding, sanding and deburring, which are typically carried out manually on welded components such as nuclear fuel racks and tube structures.
Ozan Gurdal, Nuclear AMRC research engineer (
www.namrc.co.uk), said: “The idea of the Coroma project was to use robots to automate these processes with sensor and software assistance.
"We developed an integrated end effector for the robot with a Micro-Epsilon 2910-100 BL laser profile sensor on one end and a pneumatic spindle on the other — to eliminate the need to use a tool-changing system.
"It is not possible to use the part’s design CAD model when it comes to programming robots for weld grinding or conditioning, as there is a significant difference between the design and actual part; distortion and/or warpage is inevitable after welding, so exact weld sizes are unknown.
"The 3-D CAD model of the as-welded part is required to program paths accurately.”
"The ScanControl 2910-100_BL laser sensor held by the end effector is used to scan the areas of interest in the part, which are welded joints and planar surfaces used for reference.
"The sensor provides the axial and lateral distance (2-D) measurements between the scanned object and the sensor frame, which is not sufficient for reconstruction.
"The 2-D data obtained from the laser sensor is combined with the position of the robot flange, which is read in real time from the robot controller, using a LabView-based central controller.
Combining these two, the central controller generates the 3-D reconstruction of the as-welded part as a point-cloud and converts it into the desired CAD format.
"The 3-D CAD model of the as-welded part is then used to generate grinding/deburring paths either offline or online, using in-house-developed path generation algorithms.
"Once path generation has been completed, the grinding or deburring operation begins.”
The robot used for this work was a six-axis Staubli TX200, as Staubli was one of the partners on the project.