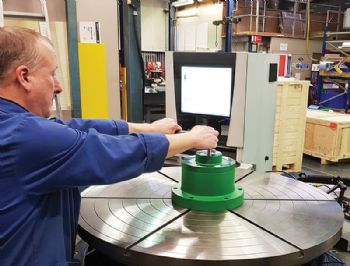
Bath-based RPI UK, which develops and manufactures precision positioning devices for high-accuracy rotary and angular
inspection systems, has installed two integrated rotor measurement and assembly platforms (iMAPs) at the Rolls-Royce-approved maintenance, repair and overhaul (MRO) facility of Atlanta-based Delta Airlines.
In addition to the iMAPs, RPI has also supplied Trent series 03 and 04 module tooling sets, significantly reducing set-up times and helping to improve the overall performance of the measurement process. Delta carries out MRO of all Rolls-Royce Trent engines in the USA.
Jim Palmer, RPI’s sales manager (
www.rpiuk.com), said: “We have been working with Rolls-Royce for over 30 years, so it is great news that both companies are choosing to invest in iMAPs, which have been independently verified to give significant operational improvements over traditional measurement methods.
"With world-class accuracy, our iMAP machine achieves higher levels of quality, while helping our customers to save money and resources.
"This is achieved by significantly reducing inspection times and the need for costly rotor ‘teardowns’ after poor rotor assembly optimisation.”
RPI’s iMAP is proven to reduce inspection times by 90% and to greatly improve gauge repeatability and reproducibility.
The technology is used by Delta after the engines are dismantled, to inspect each individual section of the engine for cracks, wear and distortion.
Measurements are taken (by AccuScan data acquisition software) to check that the components meet their original and regional board specifications.
Once the components have been approved, repaired or replaced, the iMAP is used for engine assembly to ensure alignment, concentricity and balance as each section is rebuilt.