FSG invests in unmanned grinding
Posted on 04 Mar 2013. Edited by: John Hunter. Read 2773 times.
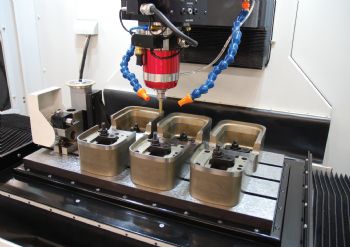
Llantrisant-based FSG Tool & Die Ltd has been providing a sub-contract jig grinding service for the past 25 years, and it has built a reputation for the quality and accuracy of its work. When the company decided to invest in a machine that could operate on an unmanned basis, it took advice from Norman Loughton, director of NL Machine Tool Consulting
(www.nlmtc.co.uk). This resulted in a visit to the Connecticut headquarters of Moore Tool Co Inc to test the Moore 500 CPWZ jig grinding machine with Fanuc 31-A control system.
Ian Slaughter, business improvement manager at FSG, says: “The first impressions of Moore were of a company that had a clear business plan to take them forward and place Moore jig grinders as the benchmark for excellence.”
The factory provided a chance to use the Moore 500 CPWZ on FSG parts, and it was clear that the build quality and attention to detail were second to none. The machine subsequently supplied to FSG has a 500mm X axis, a 300mm Y axis, a 350mm W axis and a 140mm Z axis — plus an A+B axis supplied by Lehmann; the table capacity is 300kg. Equipped with a 20-position automatic tool changer, an electric grinding-head package, a five-pallet automatic loading system and a Renishaw OMP 400 tool probe, it features a refrigerated flood coolant system, process monitoring and a motorised rotary dressing station.
The new machine has expanded FSG’s capacity and will help it to meet demand from a number of sectors — including medical, defence and automotive — for more-complex products. Potential concerns over support and maintenance for a machine from an overseas machine tool manufacturer were resolved by a support, maintenance and warranty package set up with Konecranes Machine Tool Service.