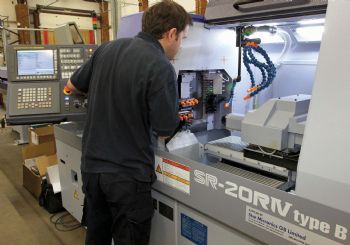
Nick Groom, managing director of Hertford-based precision turned-parts sub-contractor Qualiturn Products, has taken the unusual step of advising manufacturers, designers and purchasers on the best way to source their components from outside suppliers.
Looking first at design, he says it is often the case that unnecessarily tight dimensional tolerances are specified on drawings. In addition, modern CAD software may sometimes default to very close tolerances (typically ±10µm), which are then applied to component features — even though they are not necessary for the component’s function.
“Most features do not need to be anywhere near so precise, bearing in mind that an average human hair is large by comparison — 100µm in diameter. Stipulating very high accuracy not only increases manufacturing cost through having to reduce feeds and speeds, but also raises the cost of inspection, as more-frequent and time-consuming measurements have to be taken.
"On the other hand, loosening tolerances consistent with maintaining component functionality can greatly reduce the cost of manufacture and therefore the amount a customer is charged. Moreover, this invariably cuts the lead time from order to delivery. Further savings can be made by designing components so that — wherever possible — they can be manufactured efficiently from stock bar diameters, as this saves unnecessary cutting time.”
Dangers of over-engineering
Qualiturn is happy to provide advice on how to take cost out of a part by reducing the amount of machining needed. For example, a geometrical feature can sometimes be modified to achieve material and time savings. Indeed, working with designers and customers to solve problems and make sure designs can be made cost-effectively, while still maintaining function, is a key role for Qualiturn’s engineering staff.
With regard to the presentation of information, Mr Groom says drawings should be clean and simple. “Avoiding the use of yellow or other faint colours on drawings is beneficial, as they are difficult to read on hard-copy print-outs on the shopfloor; this may result in errors and delayed production. “When applying hidden detail lines, it is important to make sure that images do not become confusing; the designer might consider adding another view or cross-section.”
Meanwhile, Qualiturn’s production director, Steve Aulton, says the material from which components are made can be changed to reduce manufacturing cost. “For example, instead of using brass or steel and then having the components plated, it is often cheaper to use stainless steels.
“Indeed, this material is becoming increasingly popular thanks to modern methods of machining and welding it, as well as environmental concerns over plating. Indeed, stainless steel made up 50% of Qualiturn’s throughput in 2012.”
Mr Groom also says that manufacturers should ensure effective lines of communication with their customers, so that any problems — such as with a drawing or a component’s fit and function — can be overcome quickly, ensuring delivery of a product that assembles perfectly and works as designed.
Tips for buyers
Mr Groom says a buyer’s order should be complete in all respects. “It is surprising how often fundamental information is missing, like the quantity needed, delivery details and product issue numbers. If there are any special requirements regarding cleanliness that are not printed on the drawing, we need to know this before quoting, so that we can select the correct process for the parts in one of our industrial washing machines.

“The time between us submitting a quote and receiving an order can sometimes be long, which often results in the parts being needed ‘yesterday’. This time delay is sometimes unavoidable, but if it can be prevented, the customer can save money by not having to pay a premium for a rush job. Moreover, undue haste in completing an order is sometimes the cause of things going wrong, which can delay delivery. Ideally, customers should give the maximum amount of notice that is feasible for best results and lowest cost.
“The protection and handling of components during machining and transit is another consideration — one that will make a massive difference to the final look of a customer’s components. Good storage conditions while they are on consignment stock at the sub-contractor’s premises will also help to maintain future deliveries of top-quality products.”
Mr Groom also says he encourages customers to visit Qualiturn’s factory on the Mead Lane Industrial Estate in Hertford as often as they like. “In practice, the companies we work for normally keep us at arm’s length and rarely call in, but I think it is a missed opportunity. Manufacturers should work more closely with their suppliers to get the best out of them. For example, if a designer or quality manager sits around a table with Qualiturn staff, a resolution to problems and effective value engineering can be accomplished quickly.
“Moreover, if buyers visit us, they can see the entire sub-contract operation at first hand and see machines turning out batches of simple to complex mill-turned components — 24/365 — in batches ranging from 10 to hundreds of thousands. They will be in a better position to understand what makes the supplier tick and will be able to see how long it takes to set a CNC sliding-head or fixed-head lathe for a new batch run.”
Qualiturn highlights
Highlights at Qualiturn’s facility include an automated bonded storage system for raw material and finished goods, plus a similar store for tooling. Computerised production control — driven by a unique works order number for each job — provides traceability from order to delivery. This software system also encompasses quotations, sales order processing, purchasing, stock control, CAD/CAM, workshop scheduling, tool management, quality, certificates of conformity, and finance.

“If I were buying parts from Qualiturn, I would want to see resilience across all key areas of the operation — and continued investment in modern CNC plant,” says Mr Groom. “This is exactly what we do here, as we do not plan to keep any machines that are older than 10 years.
“We now have 19 Star sliding-head mill-turn centres with bar capacities up to 32mm, including one of the latest SR-20RIVs with 41 tools — installed just before Christmas. Production cost savings made as a result of using this and other modern plant are passed on to customers.
“The skill levels of our staff have gone up over recent years to match the growing plant list and level of business. Lately, the extra people employed have been apprentices. Indeed, Qualiturn has long had a policy of training setter/operators internally to ensure that they are familiar with the company’s machines and procedures, and hence are productive sooner.”