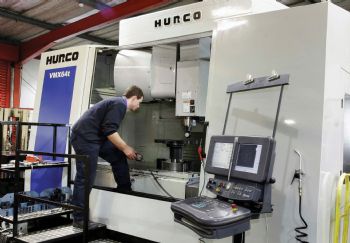
Cumbernauld-based Cowie Engineering was started by Rodger Cowie in 1999, but he went three months without any work before a manufacturer in the bottling industry ordered a batch of components, which he produced on manual mills and a lathe.
This first order was soon followed by a contract to machine fireproof switchgear cabinets for the mining sector. In 2006, Mr Cowie doubled the size of his factory; he doubled it again at the end of 2011. Now employing 13 people — including wife Cathie, daughter Julie and sons Grant and Ross — the company has just taken on its first apprentice and plans to add one every year to address the lack of skilled machinists in North Lanarkshire.
At least half of the sub-contractor’s throughput — and sometimes as much as 70% — involves machining stainless steel. Most of the machines used by Cowie Engineering are from the one supplier — Hurco Europe Ltd, High Wycombe (www.hurco.co.uk). The first of these machines — a second-hand vertical machining centre with a 1 x 0.5m table — was installed in 2001, when Mr Cowie secured additional work making fixings to support glass walls and brass frames (these have been used widely in Scotland and beyond on projects such as the refurbishment of the Rosslyn Chapel, south of Edinburgh, and the Municipal Buildings in George Square, Glasgow).
Mr Cowie says: “I knew the capabilities of Hurco machines and their conversational control system from previous employment. As I was producing mainly one-offs and small batches up to 50 parts maximum, I bought a used 1989-built Hurco BMC25, which was quick to program and ideal for those quantities. We carried on using it until the end of 2011, when it was replaced by a new Hurco VMX30.” Because the BMC25 had been so reliable, Mr Cowie decided to standardise on machines from the same supplier; he currently has seven Hurcos — including a lathe with a 10in chuck. This has Windows-based WinMax conversational programming software, similar to that used in the latest machining centres.
Retained business
Part of Cowie Engineering’s success is the result of building a loyal custoemr base; by and large, when new work is won, it represents a net increase in turnover; and now, some 13 years on, the company continues to supply its first two customers. Moreover, as the years have gone by, the switchgear components — first produced for the company’s second customer — have increased in size, prompting the purchase of a Hurco BMC4020 in 2004, and an even larger machine five years later: a VMX64 with a fourth axis.
“Once the four-axis machine was installed, we did not need to seek work for it; new business found us. One of the first jobs was the manufacture of 2,500 military parts in mild steel, each weighing around 26kg and requiring about a 40min cycle. Using the fourth axis allowed us to complete the job in one hit, whereas the lead sub-contract machinist was having trouble trying to produce the part in three operations on three machines. Despite tolerances as tight as -0/+0.03mm on hole position and 0.05mm concentricity of bores, only two of our components needed re-working.”
Software options chosen by Cowie Engineering for its latest WinMax control software include Swept Surface, which allows a 2-D surface to be moved along a contour to create complex, smooth, 3-D geometries within one conversational data block. For more-simple surfaces involving the rotation or translation of a 2-D profile, the 3D Mold feature optimises milling tool-paths to achieve good surface finishes with fine step-overs. In the rare instances when programs are prepared off-line or CAD files are supplied by the customer, data is downloaded to the appropriate Hurco machine as a DXF file, which the Ultimax controls can read directly.
In early 2011, Mr Cowie installed his first CNC lathe — a Hurco TM10. It was bought to streamline the production of mainly small batches of components (up to 30 maximum); this machine has been very busy since it was installed, tackling around 35 different jobs a month (one defence contract involved machining pipe fittings in bronze and nickel alloy).
More recently, a new customer in Aberdeen has begun to regularly order hydraulic couplings in 316 stainless steel; these are turned on the TM10 and completed on one of the company’s two Hurco VM1 machining centres.
Cowie Engineering’s burgeoning business has resulted in working 60hr weeks ( including over-time) for the past two and a half years. Mr Cowie says that if thousands of firms around the UK followed his example by keeping customers happy and continuously finding new business, while installing good quality plant and investing in people to operate it, the rate of recovery and re-balancing within the UK economy would be accelerated.