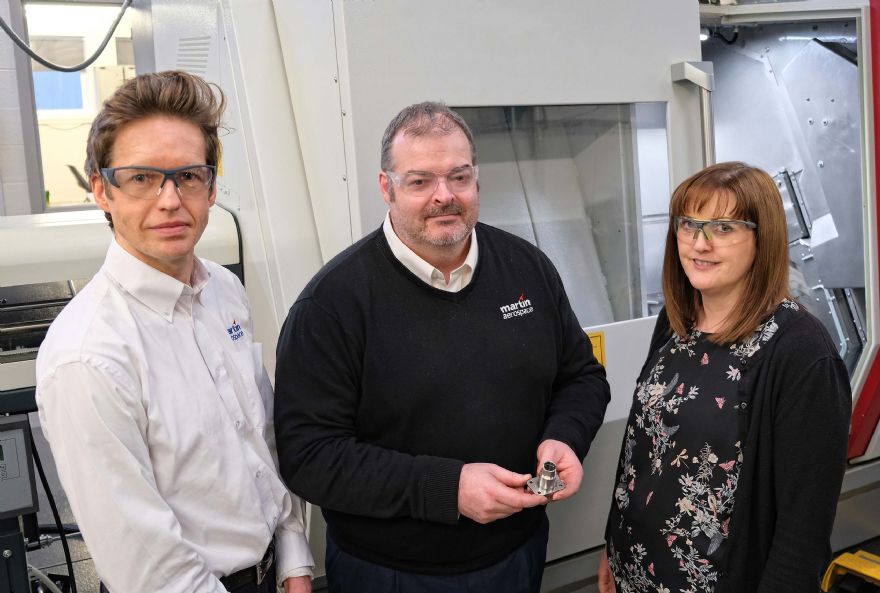
If a manufacturer plans to undertake the rigorous turning of ‘demanding’ materials such as titanium and nickel alloys, rigid and powerful lathes are required. Moreover, care must be taken over machine selection if the intended applications require the use of a sliding-head machine for turn-milling, as these tend to be less robust than fixed-head lathes.
With this in mind, Lanark-based Martin Aerospace chose a German-built Traub TNL32-9P — supplied by Gosport-based Kingsbury (
www.kingsburyuk.com) — for its latest investment in sliding-head turning technology; at the beginning of 2018, this machine started producing aero-engine components from titanium, Inconel and stainless steel 24hr a day, five days a week.
This machine proved so successful for Martin Aerospace that the company had no hesitation in returning to Kingsbury for a fixed-head lathe — a Traub TNX65 that was installed in July 2019 and is currently machining parts from Inconel and Nimonic alloys.
Both lathes have reduced multiple operations to one-hit production, making it much easier to hold the required tolerances; these are generally to within ±0.01mm, although one pin diameter is turned on the sliding-head lathe to ±4µm.
At the same time, process cycle times have been shortened dramatically — by over 90% in one case on the TNL32-9P and by typically 70% on the TNX65 — while handling time and work-in-progress have been eliminated.
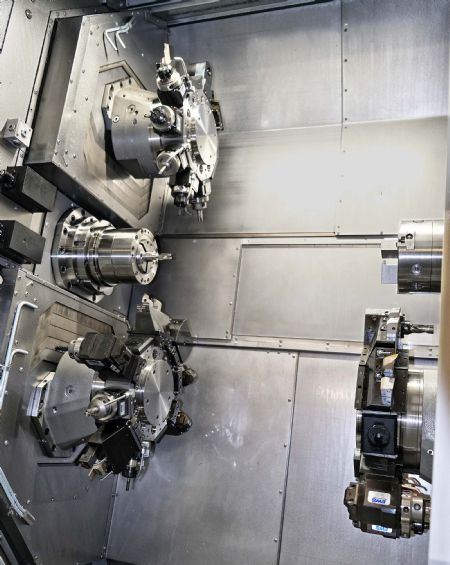
Such significant savings are partly a result of the ability of both machines to have three tools in cut simultaneously, each with a different feed rate for optimum metal removal.
Neil Lawson, operations director at Martin Aerospace, said: “In 2017, a customer increased its annual requirement for five different parts, with quantities rising from a few hundred to 6,500 per part.
“We were making them on a variety of twin-spindle turn-mill centres — both sliding- and fixed-head types. Such a sharp increase meant investing in a new turning centre to meet the demand, and a sliding-head lathe was appropriate in view of the shaft-type proportions.
“I went on-line to review what was being used for machining our tough materials, and Traub kept appearing in searches — often with reference to medical applications.”
Mr Lawson visited Kingsbury’s Gosport technical centre, where a TNL32 was available for trials. He was impressed by the robustness and capability of the machine, and by the cutting strategies proposed by Kingsburys applications engineers — especially the way they balanced the cycles at the main spindle and the counter-spindle using the machine’s two turrets.
In a demonstration, what had been a two-operation cycle time of 6.5min was reduced to a single 1.2min operation on the Traub. In another case, a 55min three-operation cycle time was cut to one 15min operation.
This demonstration was so compelling that Mr Lawson ordered the machine that same day; four weeks later it was being commissioned on the shopfloor in Lanark. It now produces all five parts from bar to a process capability of Cpk 1.67 (underpinned by 100% inspection) before they go for grinding and thread rolling.
Over the life of one tool cutting edge or insert, the dimensions of features produced on the Traub sliding-head lathe do not vary by even 1µm. Another component produced by Martin Aerospace and required in increasing quantities is a nozzle for a borescope.
Machined from an Inconel billet 63.5mm in diameter x 70mm long and weighing 2.7kg, this took 147min to complete seven operations on horizontal and vertical machining centres and lathes, during which the weight was reduced to 0.7kg.
By transferring the the job to a twin-spindle turn-mill centre already on the shopfloor at Lanark, the cycle time was cut to 65min in a single operation (this machine could have two tools in cut simultaneously, deployed by the two tool carriers).
Fixed head latheTo cope with ever-higher volumes — and with an eye to raising productivity further to reduce the unit price for the customer — Mr Lawson again visited Kingsbury, where the applications team programmed the borescope part and demonstrated it being machined by a Traub TNX65 fixed-head lathe in one hit in just 25min — a further cycle time reduction of more than 60%.
This was achieved through a combination of using the 10-tonne machine’s powerful spindles at higher speeds and feeds, using live tooling, the ability of the triple-turret configuration to have three tools in cut at the same time, and the advanced cutting strategy developed by Kingsbury.
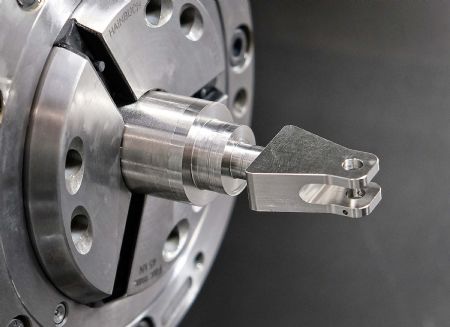
This strategy not only balanced the cycles between the two identical spindles but also overlapped dissimilar operations using two tools at the same spindle, such as turning an outside diameter while drilling an axial hole.
A second component currently produced on the TNX65 at Martin Aerospace — this time from 32mm bar fed from an LNS Quick Load 80 S2 magazine — is a Nimonic pin that is completed in a single 15min cycle.
It previously required two operations — on a turn-mill centre and a vertical machining centre — that took a total of 50min.
Summarising the company’s two Traubs, which Kingsbury supplied as turn-key packages and are programmed using Traub’s off-line CAM software, Mr Lawson said: “Both are ideal for the efficient production of parts in high volumes from tough materials, and they are platforms for continuous process improvements. This has allowed us to secure additional work, as we can provide significant savings to our customers.”