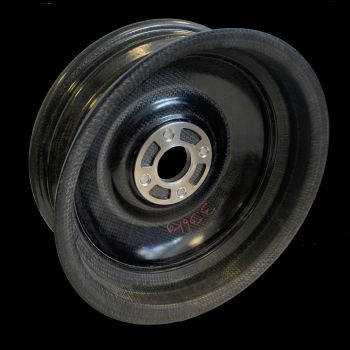
ACRIM-Wheel, the world’s first commercially viable low-cost, lightweight all composite wheel for ‘niche vehicle’ and electric-vehicle applications, is moving to the next phase of development with the manufacture of fifty wheels by the end of the year.
Furthermore, three full vehicle sets are destined for proving on MOTIV, an autonomous mobility vehicle using Gordon Murray Design’s iStream Superlight technology.
The consortium ‘delivering the wheel’ —
Carbon ThreeSixty , Far-UK, Composite Integration and CNC Robotics, alongside Bitrez Ltd as the preferred resin formulator — have completed the second phase of the programme.
This is the development and validation of proof-of-concept ACRIM wheels and confirming the feasibility of achieving significant cost reductions over existing global market offerings.
The consortium says its development offers a significant weight reduction — of 50% on a 15in wheel, for example. This weight saving would deliver a 5% fuel saving for a petrol or diesel vehicle.
For the next phase, which started this summer, the consortium aims to lower manufacturing cost and cycle time with a multi-strand approach.
This includes: processing of a three-component epoxy resin system with an in-mould release agent; piston-pump technology to deliver repeatable and higher quality lamination through increased control and monitoring of the preconditioning of resin prior to injection (metering, mixing, pre-heating and degassing); and a mould-pressure closed-loop control system to improve yield.
The project also aims to prove that robotic machining can be sufficiently accurate and repeatable for secondary machining and final trimming.
Edward Allnutt, managing director of Carbon ThreeSixty, said: “The world’s first all-composite wheel for electric and niche vehicles has moved a major step forward, and we can confidently say it has the ability to deliver huge cost savings over anything on the market.
“It can also be manufactured in volume and gives OEMs huge flexibility in what they can specify. This is truly a quantum leap in wheel design and manufacture.”