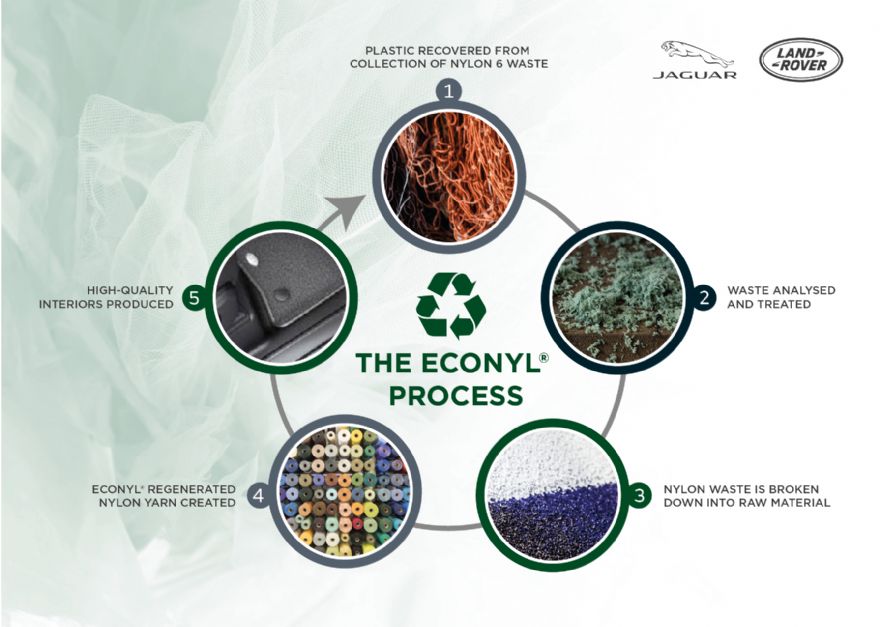
Coventry-based
www.jaguarlandrover.com Jaguar Land Rover (JLR) is working with Econyl nylon to develop high-quality interiors made from ocean and landfill waste.
Next-generation JLR models will feature floor mats and trims made with Econyl fibre from recycled industrial plastic, fabric offcuts from clothing manufacturers, fishing nets from the farming industry, and those abandoned in the ocean– known as ‘ghost nets’.
This commitment to designing sustainable luxury interiors using responsibly sourced and recycled materials is part of JLR’s Destination Zero mission, with innovation helping to make environments safer and cleaner while offering customers a premium, sustainable option.
The Econyl regenerated nylon, created by Aquafil - a global leader in the synthetic fibres industry, has already been used by high-end fashion, sportswear and luxury watch brands to create handbags, backpacks, swimwear and watch straps.
The nylon waste is reclaimed by Aquafil from all over the world. In a single year, the company recycles as much as 40,000 tonnes of waste, with the recycling process reducing the global warming impact of nylon by 90% compared with the material produced from oil. For every 10,000 tonnes of Econyl raw material produced, 70,000 barrels of crude oil are saved and 65,100 tonnes of carbon emissions equivalent are avoided.
Inside ‘state of the art’ treatment centres the waste is analysed, treated and prepared to feed into a chemical plant, where the nylon waste is broken to its original raw material using a chemical treatment process, known as depolymerisation. The raw nylon material is then turned into the yarn, known as Econyl.
Throughout the process, other by-products such as non-nylon, metallic materials or copper sulphate which is used for preventing seagrass growing on fishing nets, are removed and sent to alternative industries for recycling.
The resulting ECONYL® regenerated nylon polymer has the same chemical and performance characteristics as raw fossil material, allowing it to be processed into a fibre for carpet flooring and textiles.
This yarn can then be used to manufacture floor mats for future JLR models with the goal of using more environmentally conscious and sustainable materials while still providing customers with a premium and hardwearing product. The process is helping JLR move towards a circular economy as part of its journey to Destination Zero.
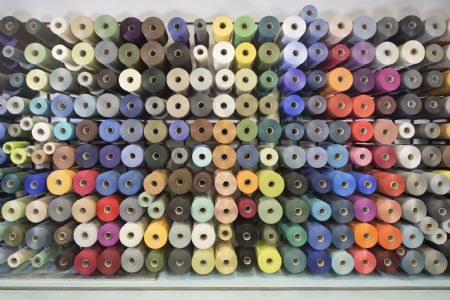
Adrian Iles, senior engineer of interior systems at JLR, said: “Our designers and engineers are committed to developing the next generation of sustainable materials that will feature on future JLR models.
“We place a great deal of focus on the creation of new sustainable materials, using the latest, most innovative techniques and textiles.
“Minimising waste, re-using materials and reducing carbon emissions sits at the heart of our Destination Zero mission. This pioneering materials research is one of the key ways we’ll achieve this and is an integral part of our design offering to our customers.”
Earlier this year, JLR was certified for the second consecutive year by the Carbon Trust, confirming business operations across the UK have met the internationally recognised standard for carbon neutrality, known as PAS 2060. Together, these UK based sites represent 77% of JLR’s global vehicle production.
Currently, Land Rover offers a premium Eucalyptus textile interior on the Range Rover Evoque while Evoque, Range Rover and Jaguar’s all-electric I-PACE benefit from optional Kvadrat – a high-quality material that combines durable wool with a suede cloth made from 53 recycled plastic bottles per vehicle.