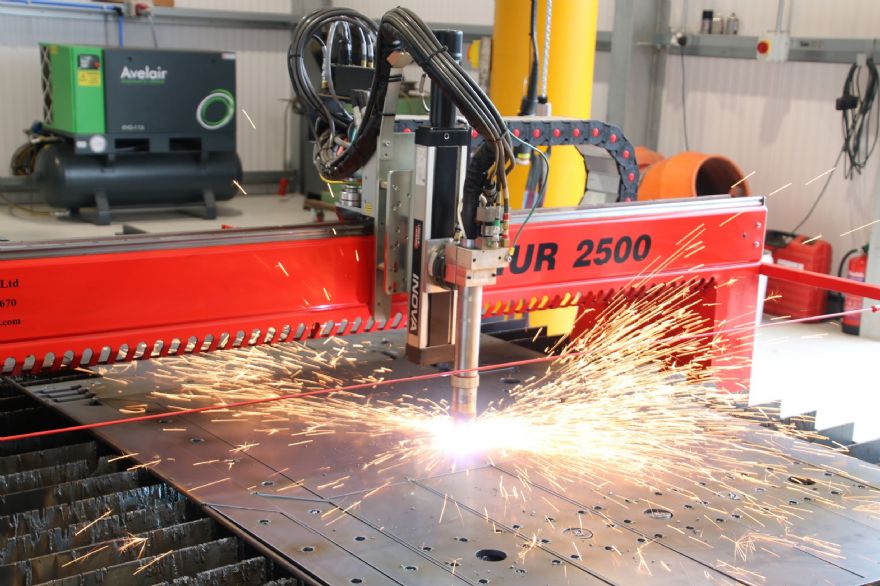
While Rochdale-based
Kerf Developments has been building plasma, oxy-fuel and waterjet cutting machines since 2002, the company started as a service-based organisation repairing and upgrading a broad range of profile cutting machinery.
It was the experience gained working on such a variety of equipment that formed the basis of Kerf’s current machine range.
Managing director Dan Taylor said: “With a considerable amount of experience in the industry, we could see which machine configurations gave the best and most reliable performance; and being completely independent we can select best-in-class products for our turn-key solutions from leading global partners such as Lincoln Electric and Burny.”
In addition to offering a standard range of profile cutting machines, Kerf works with its customers to design and build bespoke machines, which can be up to 4m wide, ‘almost any length’ and with a combination of plasma and oxy-fuel heads.
As part of its ongoing development programme, Kerf has also evaluated the capabilities of CAD/CAM and nesting software from a number of suppliers, as such systems were increasingly being requested by customers as part of a turn-key supply.
Kerf is now offering the Lantek Expert system (
Lantek — has over 24,800 customers in over 100 countries and 20 offices in 14 countries, including a team of engineers in the UK).
Mr Taylor said: “All our field service engineers have a copy of Lantek Expert software as part of their toolbox so that they can provide an instant response to any queries.
“Lantek provides regular updates to the software and is always on hand to provide online support. Moreover, Lantek has been working closely with the Kerf engineering team to perfect our UltraSharp technology.”
This ensures high-quality parts with a square edge, better quality edges and 1:1 hole sizes. For example, a 5mm-diameter hole in 5mm material, which would not previously have been possible on a plasma machine.
“The UltraSharp technology involves internally enhanced software protocols. For example: tightly controlling the acceleration and deceleration of the torch at tight contours and holes; controlling the power, gas pressure and flow accordingly; and automatically selecting special lead in and lead out configurations.
“The result is a constant and true arc with no lag between the top and bottom of the material being cut. All the parameters required to achieve this are built into our technology tables making it easy to achieve high-quality components direct from the CAD data.”