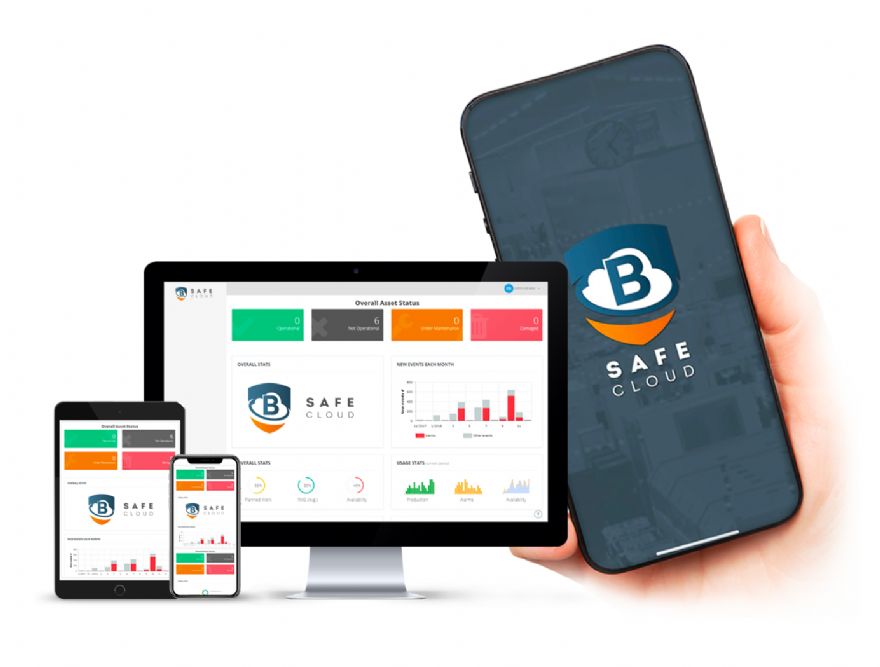
For any machine shop, the healthcare of its spindle is the lifeblood of the business — if spindles aren’t turning, then the business is not producing parts and generating revenue. With this in mind, the
Engineering Technology Group (ETG), a leading supplier of machine tools in the UK, can now offer UK customers the new B-Safe solution from Balance Systems which has been created to expand spindle and machine tool diagnostics according to vibration and temperature analysis.
The miniaturised system can be installed directly onto the spindle of a machine tool to guarantee real-time monitoring, as well as reducing the machine downtime by predicting malfunctions and potential failure.
Based upon fully customised solutions from ETG, B-Safe also has an overload alarm, an overheating alarm with programmable thresholds that correlate with real-time data of process monitoring. Additionally, it can create a collision alarm within 0.001sec – and therefore immediately stop the machine
As a company that has thousands of UK machine tool installations, ETG appreciates the concerns of the industry to protect their assets with efficient spindle monitoring. It is this customer care and full-service support philosophy that has driven ETG to introduce a complete spindle monitoring system that assesses mechanical stress and wear as well as providing a maintenance schedule for preventative maintenance planning.
The B-Safe solution can be easily retrofitted to virtually all machine tools and spindles, offering peace of mind for manufacturers as well as the productivity benefits from identifying and monitoring periods of spindle inactivity.
The system consists of a B-Safe sensor with a connector or integrated cable, a UPS and TCP-IP connection device interface, a start-up kit with software and user manual, a wide range of extension cables and M5 to M12 adaptor and magnetic support that can all be easily deployed.
Depending upon the requirements of the end user, ETG can provide a range of options to suit every manufacturing business — the flexible B-Safe System can be configured by the customer selecting the options they want.
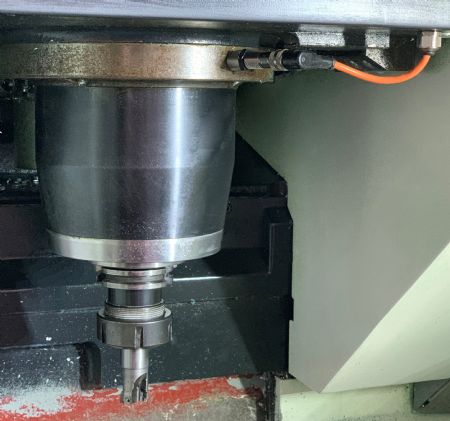
These include an event logbook, triaxial real-time data recorder, high-frequency monoaxial data, FFT analysis, a collision waveform recorder, historical trends, spindle check-up, service notes and the Fingerprint feature that is a B-Safe application intended for condition-monitoring of machine tool and machine tool spindle based on vibration analysis.
This information and much more can be viewed in the always-connected Human-Machine Interface (HMI) and the multi-platform software that provides users with full control from anywhere, thus obtaining the maximum results from a machine.
The B-Safe HMI is a software platform that allows interaction with multiple sensors at the same time and is available in different languages and layouts. It can be installed on PCs or machine tool control panels that run Microsoft Windows 7, 8.x or 10.
The B-Safe HMI allows the setting of coefficients and thresholds to adapt to a large variety of applications. This includes the Spindle Check-Up function, which can monitor the real health status of a spindle and display the residual working hours based on how the machine is being used by the operator.
Additionally, this data is available anywhere via the internet. All sensor data can be viewed through the B-Safe HMI in real-time or via the B-Safe Cloud app. These interfaces give users the ability to export the information at any time so that data can be managed with complete autonomy.
The B-Safe Cloud is the online evolution of B-SafeX System, which allows users to remotely supervise all B-Safe sensors installed on their machine tools to monitor productivity status. Users can personalise the alerts that can be received via SMS, e-mail or push notification on smartphones.
The presence of a microprocessor with integrated memory allows local detection and memorisation of collision phenomena, unbalances, overloads, anomalies of the working cycle, tool wear and bearings diagnostics.