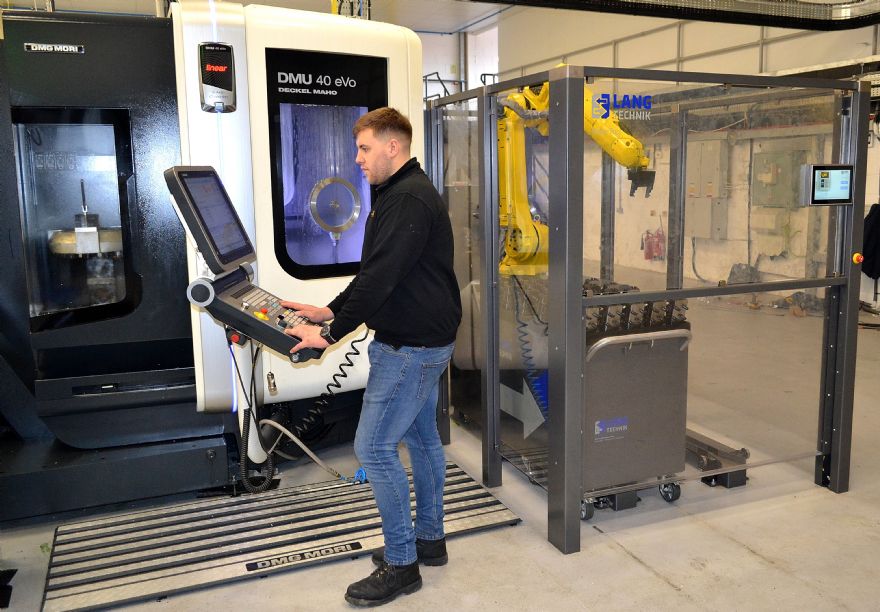
Prior to 2019, products and work-holding systems from the German company Lang Technik had been sold in the UK through a distributor, but that year
Lang-Technik UK Ltd was established in Buckinghamshire, to provide sales and application support for both existing and new customers; and in addition to achieving ‘excellent levels of sales’, over the past two years the UK subsidiary has achieved notable success installing a number of the company’s Lang RoboTrex robot systems.
The most recent installation of these systems was at the premises of
Ritchie Precision, which is based in Livingston, Scotland. In addition to other machining capabilities, the company offers five-axis CNC milling and turning services to a range of industries, including oil and gas, power generation, ultra-sonics, opto-electronics, scientific instruments, laser and medical.
The company recently had the opportunity to quote for a high-volume long-term contract related to the manufacture of intricate multi-feature medical components with ‘extremely challenging’ dimensional tolerances.
Mindful of the length of the potential contract and the fact that it could amortise some of the costs involved in purchasing the necessary equipment, Ritchie Precision investigated the most efficient methods of producing the complicated components and of achieving their demanding dimensional specifications.
Having concluded that three DMU eVo series universal machining centres from Coventry-based
www.uk.dmgmori.com DMG Mori UK were the ideal machine tools for achieving the required precision and production volumes, a cost-plan was created, a quote was tendered — and the contract secured.
The components’ accuracy specifications were such that DMU eVo-series machines were specified with a range of advanced features, such as coolant-preheaters to help eliminate the manufacturing inaccuracies caused by coolant ‘shock’. The new machines were also installed in a refurbished temperature-controlled factory.
Adding automationThe final elements that are now enabling the contract to be undertaken in an effective and profitable way, while allowing the new components to be produced in the required high volumes and within specification, are the Lang RoboTrex robot systems that now serve each of the company’s three new universal machining centres.
Essentially, these run unattended throughout the day, being fed by the Lang RoboTrex systems. Before the end of each day shift, the Robo-Trex trollies are restocked with batches of workpieces, enabling each machining centre to continue running unmanned throughout the night.
Each of Ritchie Precision’s three Lang RoboTrex robot systems uses two high-capacity trollies which are loaded with multiple vices that hold workpieces ready for machining. The systems’ robots pick workpieces from the trollies, load them into the machine tools and, when fully machined, return them. Once filled with fully machined parts, each trolley is removed, and a replacement loaded with ready-to-machine workpieces is added.
Size optionsTwo classes of RoboTrex trollies are available, each with two size options. The smaller version of the RoboTrex 52 trolley has a capacity of 30 vices (maximum part size 120 x 120 x 100mm), while the larger model has a capacity of 42 vices (maximum part size 120 x 100 x 70mm).
The smaller version of the RoboTrex 96 trolley accommodates 15 vices (maximum part size: 205 x 205 x 90mm), while the larger model has a capacity of 16 vices (maximum part size 205 x 150 x 150mm).
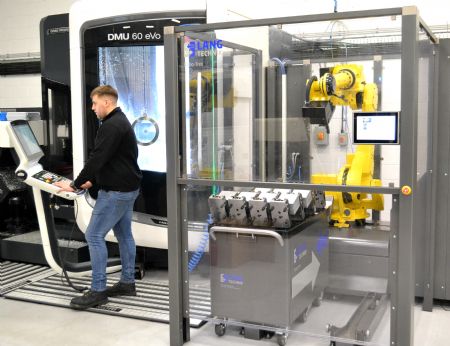
Each RoboTrex system can accommodate four trolleys. Therefore, depending on part size, the available storage capacity increases to 120/168 vices or 60/64 vices. A simple-to-operate touch panel enables easy control of the automated system; and as external access to the trolley is possible, production remains seamless as machining cycles do not need to be interrupted. Control of the system’s zero-point clamping system can be performed either pneumatically through the machine tool, or mechanically through the system’s robot.
Explaining the benefits gained through the use of Lang RoboTrex systems, Ritchie Precision’s senior manufacturing engineer Taylor Barr said: “By enabling our three new universal machining centres to work round the clock without stopping our RoboTrex systems have allowed the maximum productive potential of the machine tools to be realised and impressive volumes of parts to be produced. These automatic handling systems have provided an additional significant benefit.
“Due to the challenging specification of the parts we are producing, stopping and starting our machines can result in certain features drifting out of tolerance. As the use of our RoboTrex systems allow our new machine tools to work continuously 24/7, our machining cycles do not need to be interrupted and we avoid the scrap and rework situations caused by disrupting production.”