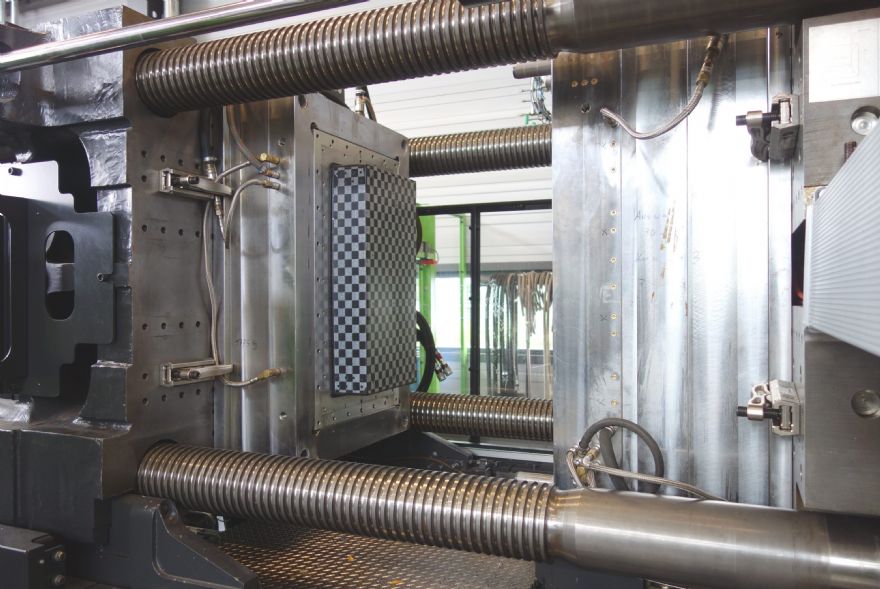
A cost-efficient lightweight battery housing for battery electric vehicles (BEVs) has been developed at
Fraunhofer LBF in Germany.
Using this, it is possible to achieve a 40% reduction in weight compared to an aluminium housing; and despite the application of fibre-reinforced plastic composites, component cost is low thanks to a specially developed manufacturing process and a ‘stress equivalent structural design’.
The mechanical properties of the housing were validated in the GHOST project (funded by the European Commission), using finite element simulations during the design phase and subsequent testing under real conditions on a test bench.
Battery packs for EVs are very heavy due to the high quantity of battery cells needed if driving ranges of around 500km are to be achieved. The mechanical structure around the cells, such as cell holders and especially the housing, which is currently made of aluminium or steel, add up to a high total weight of several hundred kg in addition to the electrical components.
Hence, despite the simplification of the electric drivetrain compared to that of internal combustion engine (ICE) vehicles, a major increase in vehicle weight can still result.
Several car manufacturers have successfully reduced vehicle weight with the help of lightweight composite construction. However, the cost efficiency of fibre composites and manufacturing processes is still a fundamental problem in automotive lightweight construction.
However, new classes of materials based on continuous fibre-reinforced thermoplastics (CFRTP) and ‘novel hybrid manufacturing processes’, are enabling new approaches, especially with regard to cost-efficient lightweight construction in electromobility.
Felix Weidmann, who is in charge of this research project at Fraunhofer LBF, said: “Thanks to an immense variety of composite structural designs, materials and manufacturing technologies, designing with fibre-reinforced thermoplastics naturally has a large potential regarding lightweight construction. However, solutions must be cost competitive and address the critical aspect of fire resistance.”
A team of researchers from Fraunhofer LBF have produced a lightweight battery housing from continuous-fibre-reinforced thermoplastics in a three-dimensional sandwich design, using an innovative process that combines high-efficiency foam injection moulding with CFRTP.
The so-called in-situ CFRTP sandwich process enables the production of finished lightweight battery housings within two minutes without the need for post-processing.
In addition, functions such as thermal insulation capability or flame resistance can be integrated in the same process step.
The housing structure consists of two CFRTP cover layers and a connecting integral foam structure in between. The cover layers consist of unidirectional tapes, which are first woven creating a cross-ply layup and then consolidated, resulting in a checkerboard appearance.
The laminate resulting from this process step is then 3-D preformed and both sides inserted into a specially-developed hybrid foam injection mould. The controlled injection of an integral foam between the laminates in this way creates the three-dimensional structure of the housing with fiber composite cover layers and a foam core.
The bonding of the CFRTP cover layers and foam core, which is of fundamental importance to the load-bearing capacity of the sandwich structure, is achieved in-situ during injection.