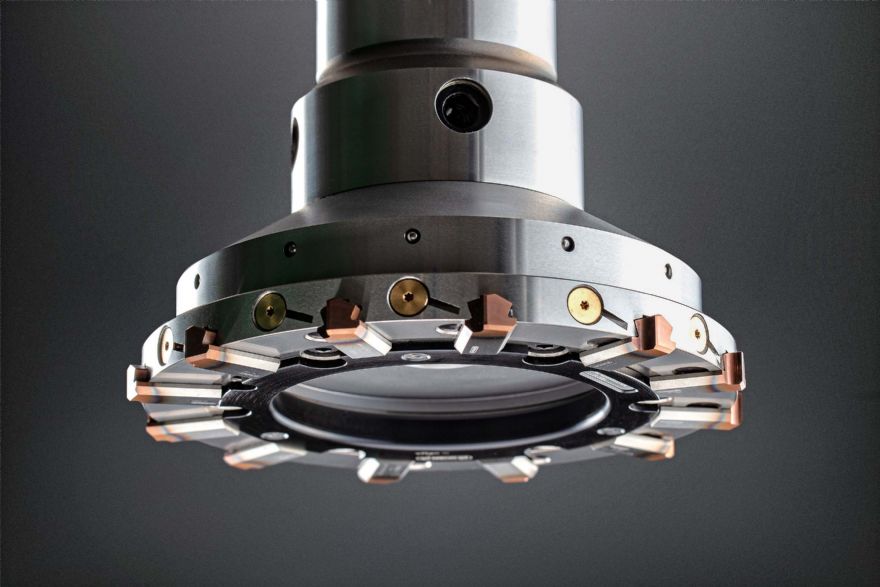
A new, modular system for reaming large-diameter holes has been launched by
Horn Cutting Tools Ltd and will be on show for the first time in the UK at
MACH 2022 (Hall 20, Stand 340). The event will take place from 4-8 April at the NEC, Birmingham.
Offering high precision, flexibility and easy handling, DR-Large reamers have exchangeable cutter heads with multiple solid-carbide inserts, resulting in ‘high cutting values’ and short cycle times.
The interface of the insert seats has been designed to offer precise interchangeability to within a few microns, so tool setting is unnecessary when exchanging the cutter head.
This interchangeable reaming system is suitable for bore diameters from 140 to 200.2mm, with six cutter heads covering the range of diameters in 10mm increments, and two sizes of head fitting on each size of reamer shank.
Moreover, a modular construction and an ABS-compatible interface means the tool can be extended to ‘any length’. All reamers are equipped with direct internal coolant supply to each cutting edge.
Also making its debut at the show will be Horn’s extended range of products for the circular interpolation milling of holes down to 8mm in diameter. The triple-edged 304 system offers a versatile, productive solution for internal groove, thread and profile milling, as well as finish boring and chamfering.
The insert has a cutting diameter of 7.7mm. Horn says that in conjunction with various vibration-damping carbide shanks featuring an internal coolant supply, the tool is more economical and versatile than solid-carbide milling cutters for machining smaller diameters.
The inserts are available in widths of 0.5, 1, 1.5 and 2mm. For milling circlip grooves, Horn offers the system with cutting widths of 0.8, 0.9, 1.1 and 1.3mm. In the case of the full radius versions, radii of 0.4, 0.6 and 0.8mm are offered.
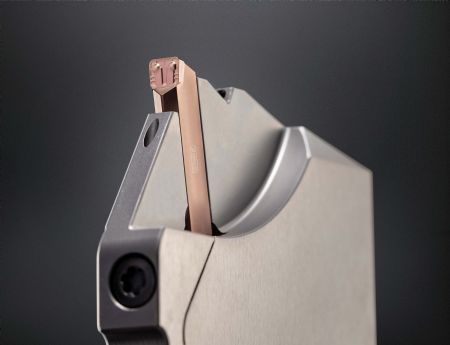
At
MACH 2022, Horn will highlight two new high-performance coatings — IG6 and SG3 — it has introduced for carbide inserts used in turning applications.
The company says that despite being less than 0.005mm thick, such coatings can extend service life by a factor of 10 or more compared to uncoated inserts.
IG6 is a copper-coloured AlTiSiN coating for machining steels in groups P and M with Horn’s S224 and S229 grooving systems.
Horn’s SG3 coating is designed for machining titanium alloys and superalloys, as well as for hard-turning and hard-grooving applications. It can withstand temperatures of up to 1,100°C.
Over the last 15 years, Horn has developed a high level of expertise in the coating of precision tools, starting with five staff and one coating system and growing to over 50 people working with 14 coating systems and the accompanying peripheral equipment.
Horn continually invests in new technologies, and in 2015, the company CemeCon delivered the first of Horn’s three HiPIMS (high power impulse magnetron sputtering) systems, which was the first in the world.
Making its UK debut will be Horn’s expanded DS range of solid-carbide end mills with a new geometry for the high-performance milling of high-strength steels at elevated material removal rates.
Different helix angles create an irregular tooth pitch for smooth machining, an optimised face geometry reduces the cutting pressure during linear or circular ramping, while improved chip spaces ensure optimal process reliability during chip formation and removal.
The end mills are available in diameters from 2 to 16mm as standard, with four or five flutes.