MACH 2022, taking place at the NEC, Birmingham, from 4-8 April, will mark the UK launch of the D200Z five-axis vertical-spindle machining centre from the Japanese machine tool builder Makino (Hall 19, Stand 120 and 130), which is represented exclusively in the UK and Ireland by
NCMT .
The machine will cycle through a reflector mould program and demonstrate Makino’s iSetup — an on-the-fly probing solution. Featured are a 30,000rev/min spindle and integral, direct-drive table for full five-axis machining.
This capability combines with high-speed SGI.5 motion control software in the Makino Professional 6 CNC to maintain tight tolerances and high levels of quality, while ensuring the accurate blending of 3-D surfaces — even during simultaneous five-axis motions.
The compact D200Z has a work envelope of 350 x 300 x 250mm and accommodates workpieces up to 300mm in diameter x 210mm tall and weighing up to 75kg; the rapid-traverse and maximum cutting feed rates are 60m/min.
The machine uses a lightweight B-axis structure with 0 to +180deg of tilt; and both this and 360deg C-axis table feature direct-drive motors for accurate, high-speed operation.
Also featured are core-cooled ballscrews, and an HSK-E50 spindle with a core and jacket cooling system to control thermal growth, deflection and vibration during high-speed machining operations.
Meanwhile, the speed and agility normally associated with a 30-taper production centre has been built into Makino’s new a40 SE — an HSK-A63 four-axis horizontal-spindle machining centre (HMC) featuring high rates of change of axis acceleration (jerk).
Additionally, the inertia of the 22kW (91Nm of torque) spindle is two-thirds that of the spindle in the model of a similar size in Makino’s standard HMC range. Designed for taking light cuts from near-net-shape non-ferrous components, the a40 SE is aimed at high-volume producers and users of aluminium and zinc die castings.
The work envelope is 560 x 640 x 640mm, the rotary table has 0.001deg indexing and a maximum table load of 400kg, and various automation options are available to reduce cost per part still further.
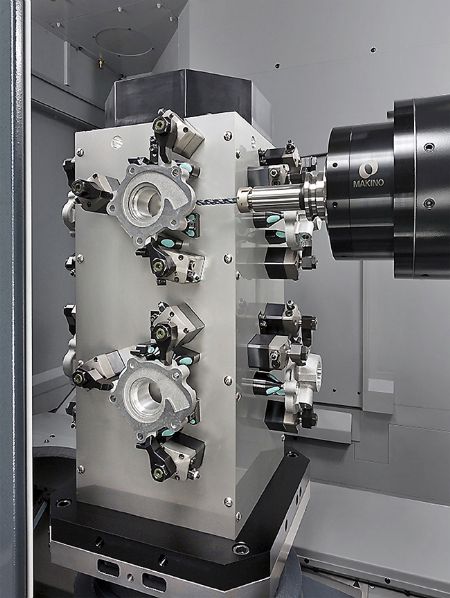
The direct-drive spindle accelerates from zero to 20,000rev/min in 1.5sec, and the elevated speed allows the use of PCD tooling and fine drills — and rigid tapping at 6,000rev/min. Furthermore, Makino’s ‘inertia active control’ evaluates component, fixture and tool weights to increase axis acceleration as the load on the table and tool weight decrease.
Vision-type broken tool detection supports unattended operation by validating the condition of the cutting tool after each tool change.
Also at the show will be MPmax, Makino’s Industry 4.0 package of software tools for real-time process monitoring and data management. With the ability to connect a multiple-machine network to a centralised computer, it allows manufacturers to retrieve, store and analyse high volumes of data in real time, enabling detection of and reaction to bottlenecks on the fly.
Also new from Makino will be a wire-cut electric discharge machining (EDM) centre, the U6 HEAT Extreme, which in addition to using standard wire from 0.1 to 0.3mm in diameter can, as an option, run a coated 0.4mm wire — the ‘largest diameter wire of any machine on the market’.
The extra wire thickness, together with the use of a second, booster generator in the machine, allows two- to three-times greater productivity and heavier duty machining compared with using a standard 0.25mm wire.
Thicker wire also allows a slower unspool speed, so there is no increase in wire consumption rate. Areas of application include aerospace and medical component machining, separating additively manufactured parts, machining tall moulds and dies, and tackling tough nickel alloys.
Two further Makino EDM machines will be on show. One will be a second wire-cut machine, the U3i, which can incorporate automation options that include a collaborative robot (cobot) for loading and unloading.
The other will be an EDAF3 die-sinking EDM machine, which will be shown eroding seal slot features and side sparking as well as demonstrating surface finish and vector machining.
Completing the exhibits on the stand will be the photo-activated adhesive system Blue Photon, for which NCMT is the sole European agent. The system is ideal for securing awkwardly shaped parts to allow maximum access to tools for tight-tolerance machining or inspection.
It can be used, for example, for clamping a turbine blade to enable the fir-tree and wedge face on the root as well as the shroud end features to be machined in one hit without tolerance build-up.