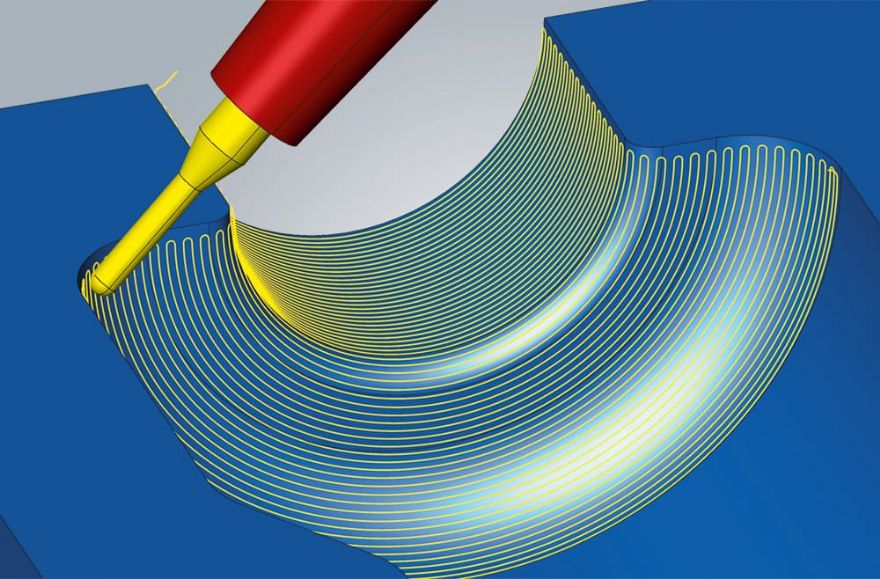
Bicester-based
Open Mind Technologies UK Ltd will be showcasing HyperMill version 2022.1 at
MACH 2022 (Hall 17, Stand 440), and demonstrating why it is a complete solution for everything from three-axis machining to complex five-axis working; and while there will be new developments for enhancing productivity, performance and programming times for components produced on machining centres, the company has also added new features for its turning cycles. The event will be taking place from 4-8 April, at the NEC, Birmingham.
The latest version of HyperMill will present two new features designed to make programming turning processes easier and faster.
Component areas for turning or plunging are recognised, structured and displayed, during which HyperMill automatically divides the recognised features into several areas that can be turned, faced, groove machined or machined with a combination of these technologies — saving users considerable time in contour selection and programming while giving them full access to all recognised contours.
The latest version also offers convenient programming for production on turning centres with a main spindle and a counter spindle. The machining jobs are simply programmed under the ‘main spindle’ and ‘counter spindle’ containers, which assigns them to the respective machining side.
DMG Mori CTX machines with a Siemens control are supported with this function in HyperMill 2022.1; more manufacturers and machine types will follow imminently.
Open Mind will also be demonstrating its automated program generation at
MACH 2022 with the HyperMill Automation Centre, which allows users to automate creating the job list, as well as the selection and positioning of clamping devices.
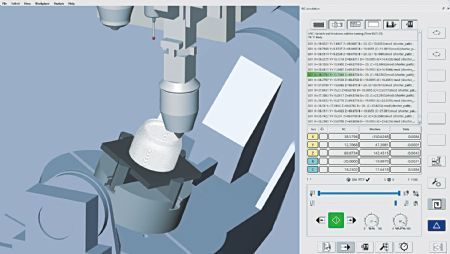
The solution primarily focuses on the individual elements of a CAD model and makes it possible to define and standardise complex processes; and once a manufacturing process has been defined, it can be applied to any new component and executed automatically.
For manufacturers using EDM technology, there are also product enhancements. Now, users no longer need to program at the controller, thanks to the simple creation and subsequent modification of traverse paths during the EDM process with HyperCAD-S Electrode. Three new modes are available to users for creating the traverse paths.
With additive manufacturing (AM) technology evolving at pace, Open Mind has further enhanced its HyperMill Additive solution. The latest version opens a range of flexible options for ‘directed energy deposition’ (DED) processes and ‘wire arc additive manufacturing’ (WAAM) in terms of highly complex five-axis simultaneous processing.
Both laser-based powder nozzle machine heads and wire arc AM can be controlled using the software from Open Mind for selective material deposition, as well as conveniently programmed and automatically simulated for collision avoidance.
HyperMill can also be applied to powder bed fusion (PBF). If 3-D printed parts do not offer the required precision, or support structures need to be removed, the components can be completed through five-axis machining.
Even hard-to-reach areas can be machined using HyperMill, which supports re-working of this nature whereby the 3-D printed components ‘are analysed, machined to size and examined’. Open Mind says it is driving forward the implementation of integrated process chains with additive and subtractive manufacturing combined in a single machine tool for hybrid manufacturing.