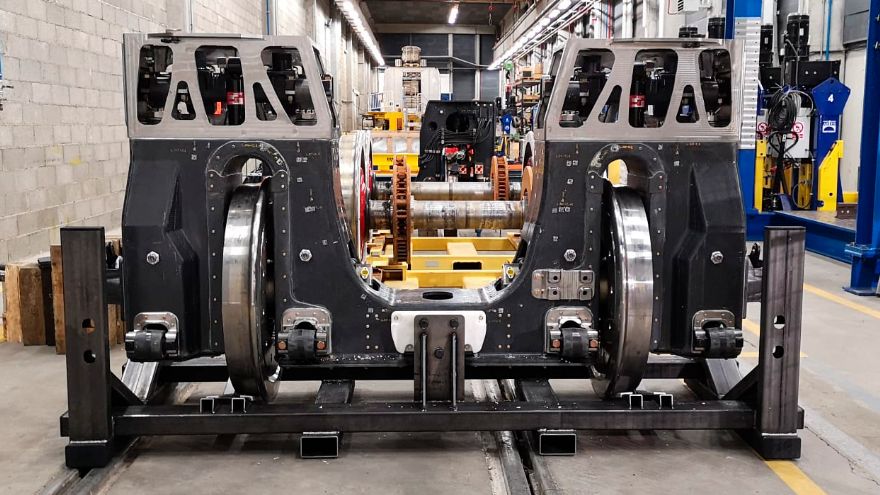
The Spanish train manufacturer
Talgo, which has its headquarters in Las Rozas, a town near Madrid, has developed a new type of its ‘characteristic’ running gear frames (Rodals), which makes it possible to further reduce the tare weight (unladen weight) of the vehicles it manufactures, starting with Avril very-high-speed trains (Avril stands for ‘Alta Velocidad Rueda Independiente Ligero’, which roughly translates as ‘Light High-Speed Independent Wheel’).
By using carbon-fibre-reinforced polymer composites (CFRP), the rolling assembly mass can be reduced by 50%, thus improving the energy consumption of the train and passenger capacity. Current running gear frames are constructed using welded steel plates.
However, both the geometry of those frames and the welding properties (mainly due to fatigue considerations) constrain the possibility of weight improvement in the frames with current materials and processes; and because this running gear is the second-heaviest structural component of the train, and the first one in terms of structural resistance requirements, Talgo says the substitution of steel with new generation composites can result in significant weight reductions with no impact for the rest of the operating requirements.
After a careful study of materials and processes, Talgo considered CFRP to be the best option for the development of a completely new concept in the rail sector. Indeed, the company has successfully finished the full-scale validation of structural requirements according to the current standards (EN 13749), including both static and fatigue tests exceeding 10 million cycles with no significant damage after NDT inspection.
The technology used to manufacture the running gear is based on hand lay-up CFRP ‘prepreg’, making it fully compliant with the most stringent ‘Fire-Smoke-Toxicity’ standards in rail transport. The next development steps will see the composite Rodal running on track, operating under real conditions for final acceptance.
In parallel, the development will also be used to gain valuable knowledge to be used sector-wide, in the implementation of a new set of standards regarding the acceptance process of new materials like CFRP in rail transport; and while the new rolling assembly has been developed using the Avril platform as a reference, it could be adapted to other Talgo intercity or commuter vehicles.