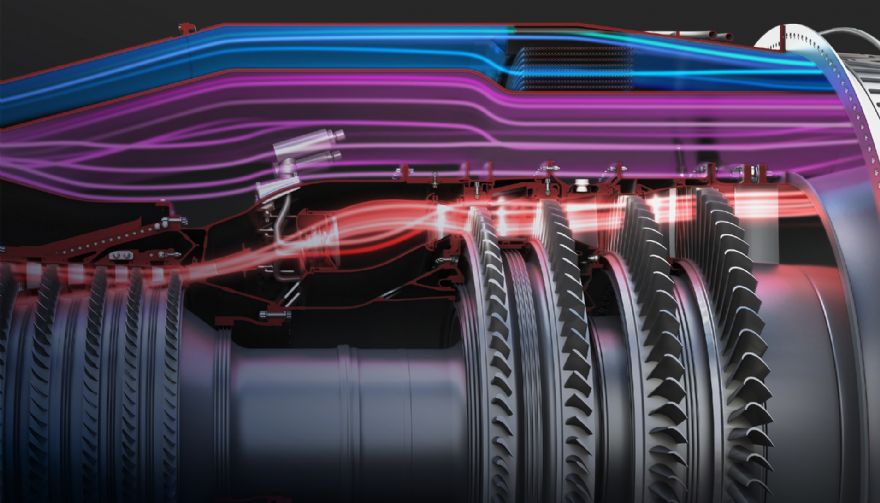
The
US Air Force and
GE Aviation have successfully concluded testing on GE’s second XA100 adaptive cycle engine at the Air Force’s Arnold Engineering Development Complex (AEDC) in Tennessee. With testing at AEDC completed, GE has accomplished the final major contract milestone of the Air Force’s Adaptive Engine Transition Programme (AETP), which began in 2016.
David Tweedie, GE Edison Works’ vice president and general manager for Advanced Products, said: “This is the culmination of more than a decade of methodical risk reduction and testing GE has completed with the US Air Force across three different adaptive cycle engine programmes.
“The engine performance data we gathered at AEDC continued to show the XA100’s transformational capability, while also demonstrating a return on substantial US Air Force and taxpayer investment. We now stand ready to transition to an engineering and manufacturing development programme and bring this engine to the field with the F-35 before the end of the decade.”
He continued: “This engine isn’t a concept, proposal, or research programme. This is a flight-weight, highly product-relevant engine that would provide the F-35 with 30% more range, greater than 20% faster acceleration, and significant mission systems growth to harness the F-35’s full capabilities for Block 4 upgrades, and beyond.
“The XA100 is the only F-35 propulsion modernisation option that has been built, fully tested, and evaluated against US Air Force performance targets, and the only option that will give it the capability it needs to outpace adversaries for decades to come.”
The XA100 combines three key innovations to deliver a generational change in combat propulsion performance: an adaptive engine cycle that provides both a high-thrust mode for maximum power and a high-efficiency mode for optimum fuel savings and loiter time; a third-stream architecture that provides a step-change in thermal management capability, enabling future mission systems for increased combat effectiveness; and extensive use of advanced component technologies, including ceramic matrix composites (CMC), polymer matrix composites (PMC), and additive manufacturing.
These revolutionary innovations increase thrust more than 10%, improve fuel efficiency by 25%, and provide significantly more aircraft heat dissipation capacity, all within the same physical envelope as current propulsion systems. GE’s engine is uniquely designed to fit in the F-35A, as well as the F-35C without modifications to the tailhook. Its improved fuel efficiency provides a significant reduction in carbon emissions and will operate on any US Air Force-approved sustainable aviation fuel.