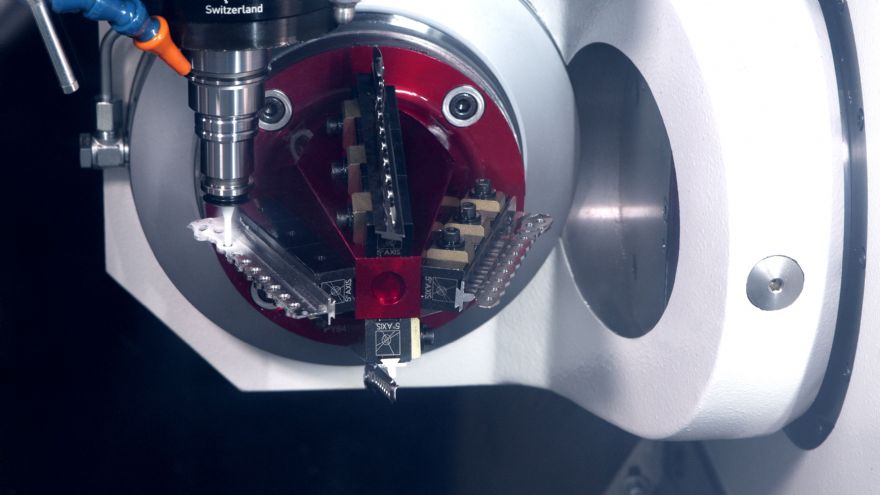
Supercritical CO
2 milling of medical plastics using a Mikron MILL S 400U (simultaneous) five-axis machining centre equipped with a Fusion Coolant Systems’ sc-CO
2 delivery system has produced impressive burr-free results in trials undertaken in Germany by
GF Machining Solutions and the Competence Centre for Machining (KSF), Furtwangen University IFC, Tuttlingen.
Ultra-high molecular weight polyethylene (UHMWPE) is a common material used in medical orthopaedics. Its durable, low-friction surface is used as a spacer that ensures mobility for knee, hip and shoulder implants. However, machining this material with traditional milling techniques results in the formation of burrs that are often removed manually in a secondary process.
In addition, as the thermal expansion coefficient of UHMWPE is more than 12-times higher than that for steels, controlling heat during machining operations is essential in order to achieve the tight tolerances and high dimensional accuracies required for implants.
In recent tests, the effects of using supercritical CO
2 cooling (sc-CO
2) for the milling of spacers, using a Mikron MILL S 400 U five-axis milling machine equipped with a Step-Tec 42,000rev/min spindle, a Fusion Coolant Systems’ Pure-Cut+ sc-CO
2 delivery system, were recorded.
Two different spacer cutting trials were conducted: slot cutting using a 3mm single-blade endmill; and five-axis milling using a 6mm ball nose endmill. The results obtained in both trials indicate a significant reduction in burr formation, improved work-piece accuracies and better surface quality. These factors point toward a more reliable machining process that may greatly reduce, or even eliminate, manual deburring.
UHMWPE can be milled dry to avoid (especially in medical applications) the introduction of contaminants and moisture absorption. Slot machining was performed ‘dry’ at a slot width of 3mm and a depth of 6mm.
Medical-grade cutting fluidA supercritical CO
2 delivery system from Fusion Coolant Systems was fully integrated with the Mikron MILL S machine. This system is capable of providing CO
2 up to 110 bar pressure and includes a Pure-Cut+ MQL (minimum quantity lubrication) delivery system. Supercritical CO
2 together with MQL is channelled through the spindle and, via small slots in the tool holder, rapidly expanding supercritical CO
2 was directed towards the cutting edges of the tool. A medical-grade cutting fluid, was introduced to the supercritical CO
2 at a rate of 0.1-0.25ml/hr.
This particular lubricant is validated for use on medical products due to its ability to evaporate at room temperature without leaving any trace residue on the milled surface. The cutting trail was repeated, and it was observed that the burr formation was significantly reduced using supercritical CO
2 compared to dry milling.
Using image processing software, a comparative analysis of the burr area was calculated and compared between dry and supercritical CO
2 milling. With CO
2 machining there was a significant reduction in burr formation of approximately 95%. In the next step of the trial, a knee spacer was five-axis machined under both dry and SC-CO
2 conditions. Again, results here revealed excessive burr formation when dry milling was used (likely due to material melting during the cutting process) as well as poor surface quality.
However, very low burr formation and a clean work-piece surface with detailed milling contours resulted using SC-CO
2 milling. The use of UHMWPE in knee, shoulder and hip implants is extensive but, as the material cannot be moulded using conventional moulding technologies, it is most often milled. In most cases the milling process created a significant number of burrs, the removal of which is time consuming and costly.
Although still being tested, it would appear at these preliminary stages that using tools with CO
2 delivers a stable and repeatable machining process for machining UHMWPE that results in a superior and finer surface finish with a dramatic reduction in burrs.