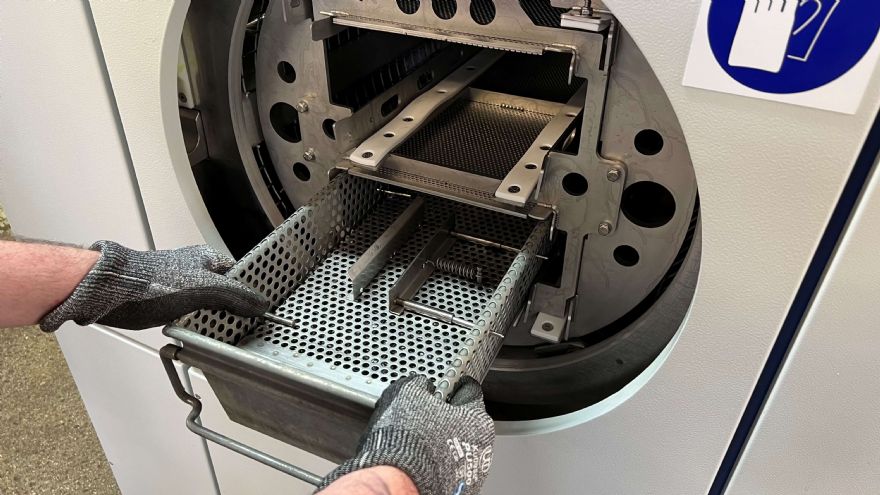
Tewkesbury-based
MecWash Systems Ltd has created a bespoke aqueous cleaning system that has revolutionised the effectiveness of the washing and degreasing programme at
APT Leicester, a leading precision mill-turned parts and CNC specialist. The upgrade from a perchloroethylene cleaning system to the MWX300 has streamlined the cleaning operation and enabled APT to simultaneously prioritise their environmental goals and increase its output, all while maintaining the highest standard of finish.
The initial research and analysis with APT Leicester allowed Paul Jarratt, sales manager at MecWash, to gauge the application and outline the machine specifications required. These discussions are essential to gain a full understanding of the geometries used and the contaminants involved. APT Leicester manufactures precision turned parts and offers CNC machining services. The business supplies turned component parts to industries, including aerospace, where the stringent requirements regarding the quality of the components requires rigorous detail at every stage of the manufacturing process.
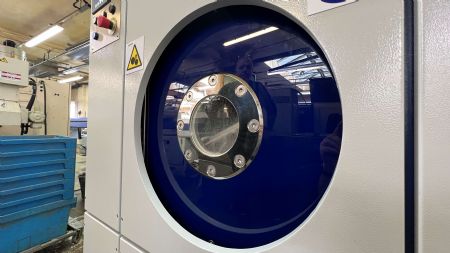
Mr Jarratt said: “APT Leicester's CNC processes primarily focus on precision machining using a diverse range of materials such as stainless steel, aluminium, brass, plastics and titanium. The MWX300 cleaning machine plays a crucial role by cleaning the mill turned parts before they are shipped to customers or undergo any additional heat or surface treatments. The former perchloroethylene cleaning system did an effective job, but APT transitioned from it due to environmental considerations.”
“The MWX300 was selected as the most appropriate system due to its compact size and powerful cleaning capabilities. The ultrasonics provide up to 30watts/litre of high-power to unsettle any contaminants from the components. The MWX300 provides an immaculate surface finish with both hot and vacuum drying functions. Due to the limited floor area available, the MWX300 was designed with roller shutter doors in place of conventional swing doors to aid access; APT Leicester was also particularly interested in adding our Aqua Save system to reduce water consumption and improve sustainability. This innovative MecWash system captures, filters, and recirculates the cleaning water.”
Sustainability credentialsAPT Leicester managing director Nick Baller said: “Manufacturing top quality mill-turned parts requires detailed cleaning, and we were confident that MecWash had the experience in manufacturing to create an efficient solution. The cleaning performance of the MWX300 has been a major step forward in our sustainability credentials. The results have been excellent, with parts that are oil free and ready for shipping. The productivity of the business has improved with the MWX300 system. We can effectively clean the turned parts that we manufacture, leaving them entirely free of oil, small swarf and debris. The system has helped to drive our mission of providing first-class, sustainable CNC manufacturing to our customers.”
MecWash managing director John Pattison said: “We were delighted to supply APT Leicester with the MWX300. This compact system is suitable for applications such as turned parts production as it is proven to clean challenging components. The cost savings and environmental benefits of an efficient aqueous cleaning process are well established. The MWX series represents the highest standard of parts washing in the market and can clean large volumes to the same continuously high standard. The experience of the team in designing and building parts washing machines for customers in sectors such as aerospace, automotive, defence, engineering and medical, gives us total confidence in meeting and exceeding the specific needs of manufacturers.”
For three decades, MecWash has specialised in the design and manufacture of a complete range of aqueous parts washing and degreasing systems. These machines are custom made to clean specific applications for the manufacturing industry. With its technical expertise and an in-house laboratory, MecWash systems are capable of cleaning metal and plastic engineering components with complex geometries, difficult substrates and contaminants, without the use of harmful solvents.