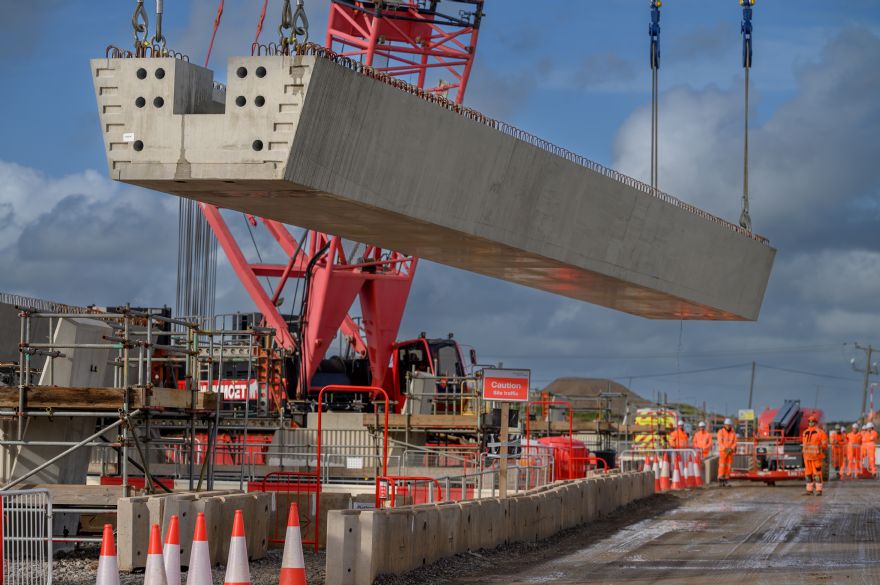
At the end of last month,
HS2 Ltd began lifting the first of 72 huge beams that will support the deck of the Thame Valley Viaduct, the first of its kind in the UK to have all major elements manufactured off site. The operation saw engineers at the site near Aylesbury use two massive cranes to lift the beams — each 25m long and weighing 90 tonnes — into position on top of the viaduct piers, ‘like giant Lego blocks’.
Instead of using a more traditional approach, with multiple smaller beams for each span, the designers opted for just two large hollow U-shaped beams per span, which allows for a lighter structure and a more-simple construction. Moreover, the lighter-weight design, ‘inspired by viaducts’ on the Spanish high-speed rail network, also reduces the amount of carbon-intensive concrete and steel in the structure, thereby cutting the structure’s carbon footprint by around a third.
The underside of the 880m-long viaduct crossing the River Thame and surrounding flood plain flood plain will be just 3m above the ground and comprise 36 even spans. The viaduct was designed by HS2 Ltd’s main works contractor, EKFB — a team made up of Eiffage, Kier, Ferrovial Construction and BAM Nuttall — working with specialist on-site construction partner FC Civils Solutions. A similar approach used for this viaduct is also being considered for the nearby Edgcote Viaduct in Northamptonshire.
Traditionally, viaduct beams — even when manufactured off-site — are secured together above each of the piers with a concrete diaphragm that is cast in situ. The larger pre-cast beams that will be used at Thame Valley can be secured directly to one another, removing the need for the diaphragm. The deck on top of the beams that will carry the track will also be made from pre-cast concrete planks; this means that every major element of the structure — the piers, beams, deck planks and parapets — can be prefabricated and slotted together.
Off-site manufacturing also helps spread contract opportunities and supply chain jobs throughout the UK, with 200 people — including apprentices and graduate engineers from nearby Universities — employed at Pacadar UK’s facility on the Isle of Grain in Kent, from where it is delivering pre-cast concrete parts for the viaduct, as well as tunnel segments for HS2’s London tunnels.