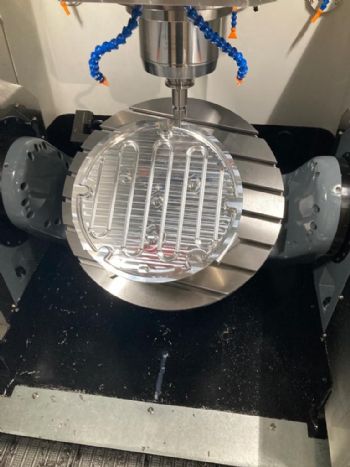
Like any fledgling company, the wind of change can blow quickly through a business, and this was certainly the case for
Shropshire Precision Engineering (SPE) Ltd. Initially set up as a part-time business, it wasn’t until technical director Robin Chisnall joined the Shrewsbury-based business in 2017 that the company set about upgrading its machine tool and cutting tool technology – with
XYZ Machine Tools and
Industrial Tooling Corporation (ITC) proving to be the partners of choice.
As an engineer who has been in the industry for almost 50 years, Robin sold his previous business for a life of happy retirement back in 2016, but when he got the call from fellow director and company founder Chris Mills a year later, his love for engineering tempted him back. The company’s three-axis machining centre and teach lathes were quickly replaced by an XYZ TC65LTY turning centre with live tooling, a four-axis XYZ machining centre and an XYZ ProTurn 425.
This reduced set ups and improved throughput drastically, so the company followed these acquisitions more recently with an XYZ UMC 600 five-axis machining centre and a fourth-axis 1100HD machine. While this investment has improved productivity and throughput, the tooling supplied by ITC has also contributed in delivering production consistency and improvements, impeccable surface finishes, and reduced waste and costs.
When the ISO: 9001 certified business was founded in 2014, the workload was primarily centred around the automotive industry. As a sub-contract manufacturer, SPE still produces components for the automotive industry as well as a host of other sectors. However, nowadays 90% of the workload is focused on serving the rapidly growing and high-demand semi-conductor sector. The company provides a complete manufacturing, cleaning, assembly and packaging service as well as testing and production control. Much of the growth in the semi-conductor market is credited to John Bradley joining the company as general manager and directing the Shropshire business toward this growth sector. To serve the high-end marketplace, lead times, precision and component consistency, as well as quality, are essential - this is why Robin Chisnall turned to ITC.
Performance and efficiencyHe said: “When I joined the company, it was primarily using cutting tools from distribution companies. The issue was a several-day lead time for some standard tools with no guaranteed delivery date. We often had to take jobs off machines because we didn’t have the tools available. Another area where this lack of consistency was frustrating was in the cutting tools themselves. A repeat order for an end mill would sometimes be a different brand, coating or geometry – this completely ruined our performance and efficiency. As I had worked with ITC in the past, I knew that its service, support and delivery times were second to none. It is also a UK manufacturer that can manufacture special tools as well as standard products. I called the local ITC representative and we set about standardising our tool library and consumption.”
A lot of components produced at SPE are small delicate stainless and inconel parts. To machine these, SPE implements ITCs 5021 Series of long length centre cutting 5-flute end mills with harmonic fluting and the 5041 Series of 5-flute extended reach end mills. Mr Chisnall explained: “Instead of changing between roughing and finishing tools, we trochoidal mill with the ITC five-flute Cupro coated tools at high speeds and feeds with a low depth of cut. The surface finishes are incredible and the tool life is 50% better than any tools we have used before. In fact, we have recently started three new machinists and they are all struggling to comprehend the remarkable tool life we get from the ITC end mills and the reduction in tool changeovers.”
The tool life is a huge benefit to SPE, as are the improved surface finishes. “Before we started using ITC tools, surface finishes were inconsistent and we used to undertake significant hand polishing – this is no longer the case. This is saving our company a lot of labour hours every week.”
From a productivity perspective, the range of ITC trochoidal five-flute end mills and also the 2152 Series of two-flute ball nose end mills that are used from 1 to 8mm diameter for steel machining, have improved throughput significantly. Mr Chisnall added: “All of our jobs are small volumes, so we can’t always track cycle times. However, when we first moved cutting tool suppliers, there were several jobs with 20 or 30min cycles that were reduced to less than 10min using ITC tools. This is a credit to the quality, performance and rigidity of the tools that enable us to run 30 to 40% faster than rival tools.”
As well as using a variety of ITC’s UK-manufactured cutting tools that range from end mills and drills through to taps and reamers, the Shropshire manufacturer has also invested in BIG Kaiser tool holders supplied by UK agent ITC.
Trochoidal millingHe added: “When we moved to ITC, we could conduct trochoidal milling at much higher feeds and speeds. However, the increased cutting forces were pulling tools from our milling chucks. To retain and extend these productivity gains, we needed high-quality chucks. We spoke with the ITC engineer and we bought the BIG Kaiser high-power BBT milling chuck with dual face and taper contact. The slim-line design gave us the reach we needed and the clamping forces eliminated tool ‘pull-out’. Additionally, the BIG Kaiser chucks improved our rigidity and stability, this allowed us to run our ITC tools at even higher speed and feed rates.”
As any engineer could imagine, the dual face and taper contact system on the BIG KAISER milling chucks from ITC goes way beyond maximising performance and creating process security for high-speed and feed applications. Surface finishes and precision are also improved.
Alluding to the quality of BIG Kaiser toolholding systems, Mr Chisnall continued: “We have a lot of tight tolerance work and one job requires a series of 6mm diameter reamed holes at a 70mm pitch. We would have to do test runs on parts like this to avoid scrap. This deviation was not down to the machine or process reliability – but the toolholders. To eradicate this issue, ITC suggested we try the BIG Kaiser MEGA New Baby Chuck for drilling and reaming the holes. We trialled a reamer with the new MEGA New Baby Chuck and it was reaming to a concentricity and precision level within 3µm. The run out of the previous chucks would never have held such tight tolerances.”
Mr Chisnall concluded: “We have guaranteed next-day delivery on standard products, excellent technical support and an unfathomable diversity of special products. In fact, with every special tool, ITC will create a product code. This means that we can order the specific code and we will get repeat orders of our special tools that are all manufactured in the UK.
“This consistency is of critical importance to us. Some of our parts have a value that exceeds £12,000 - to scrap one of these parts because of tool ‘pull-out’, or the run-out on a precision feature is outside tolerance due to an inferior collet is not acceptable for our business. That is why we have chosen ITC as our cutting tool partner.”