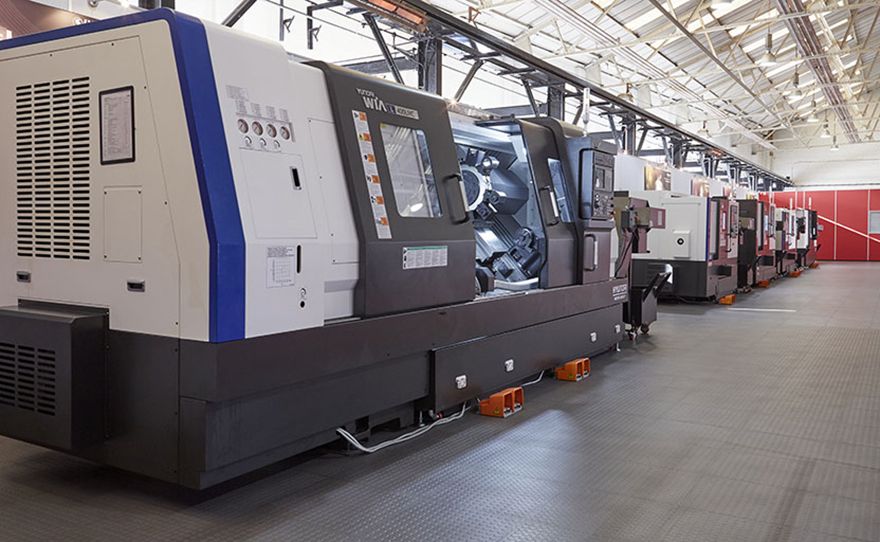
The aerospace industry, known for its stringent standards and high-stakes applications, epitomises the pinnacle of precision engineering. Central to achieving this unparalleled precision is CNC machining, a technology that has revolutionised manufacturing processes. In aerospace engineering, the role of CNC machining is pivotal, particularly when it comes to meeting precision requirements and overcoming material challenges inherent in this field.
Aerospace components are subject to extreme conditions, including high velocities, temperatures, and pressures. This demands a level of precision that is non-negotiable. CNC machining steps in as a hero, offering unparalleled accuracy and repeatability. It is not just about achieving dimensions within the ranges of thousandths of an inch; it is also about ensuring that these tolerances are maintained consistently across multiple components and production cycles.
CNC technology allows for the creation of parts with complex geometries that would be nearly impossible to achieve with manual machining. This capability is crucial in aerospace, where the aerodynamic efficiency and overall performance of aircraft and spacecraft are heavily dependent on the precision of each component. Furthermore, CNC machining plays a critical role in the prototyping phase, enabling engineers to test and refine designs swiftly and accurately.
Material challenges in aerospaceThe aerospace industry often employs materials that are difficult to machine, such as titanium, Inconel, and composites. These materials are chosen for their strength-to-weight ratios and resistance to environmental factors, but they present significant machining challenges. CNC machining, with its advanced capabilities, is adept at handling these materials.
Titanium, for instance, is notoriously tough and can lead to rapid tool wear. CNC machines, equipped with specialised tooling and programming, can manage the appropriate cutting speeds and feeds to machine titanium efficiently while minimising tool wear. Similarly, Inconel, known for its hardiness and heat resistance, requires CNC machines to perform precise and slow cuts to maintain accuracy and tool life.
Composites, another aerospace staple, pose a different set of challenges. Machining composites can lead to delamination or fibre pull-out, compromising the structural integrity of the part. CNC machining addresses these issues through controlled cutting processes and specialised tool paths, ensuring the integrity of the composite materials while achieving the desired precision.
Innovations in CNC for aerospace
Innovations in CNC for aerospaceThe future of CNC machining in aerospace is marked by continuous innovation. Advancements in CNC technology, including five-axis machining and automation, are pushing the boundaries of what can be achieved. five-axis machining allows for the machining of complex parts in a single set up, reducing the time and potential for error. Automation in CNC machining not only increases efficiency but also enhances precision by reducing human error.
CNC machining is not just a manufacturing method in aerospace; it's a critical enabler of the precision engineering that this field demands. From meeting exacting precision requirements to overcoming the challenges presented by advanced aerospace materials, CNC technology is at the heart of innovation in aerospace engineering. As the industry continues to evolve with new materials and design challenges, CNC machining will undoubtedly remain an indispensable tool in the aerospace manufacturing arsenal.
If you are on the lookout for high-quality CNC machines, contact
Ward CNC today!