PTG Holroyd has announced a significant upgrade to its 4EX-R-BL (BL stands for blower) dual-capability CNC rotor milling machine, to ensure it remains as a leading choice among manufacturers wishing to streamline their production capabilities.
Originally launched in 2015, the 4EX-R-BL was developed to satisfy a gap in the market for a rotor milling machine able to precision-mill both traditional helical compressor rotors and low-pressure output displacement compressors, such as Roots-type rotary lobe blowers. Since then, the machines have helped a number of organisations to transform the way in which they mill straight-fluted, infinite lead rotors — significantly reducing manufacturing time and increasing the accuracy of the production process.
Just as with PTG Holroyd’s recently launched HG Series of worm and helical gear grinding centres and its updated range of TG Series rotor and helical grinding machines, the upgraded 4EX-R-BL will benefit from Siemens SINUMERIK ONE future-proof CNC as standard. Fanuc’s 30i-Model B Plus CNC will be offered as an alternative.
Mechanical enhancements to the revised 4EX-R-BL models include a totally redesigned machine bed and worktable to enable components of up to 450mm in diameter to be milled. Both the bed length and bed width have also been increased to give greater support against increased cutter forces.
Additional cutter rigidityWhile further supporting the machine’s greater milling capability (the original 4EX could produce parts of up to 420mm in diameter), the machine bed height has been lowered by 150mm, with additional buttress supports providing increased stability during flute milling on what was already an incredibly robust and steady machine. The maximum cutter width has been increased from 320 to 400mm to accommodate particularly large rotor profiles, with Holroyd’s HSK 160 cutter spindle interface providing additional cutter rigidity.
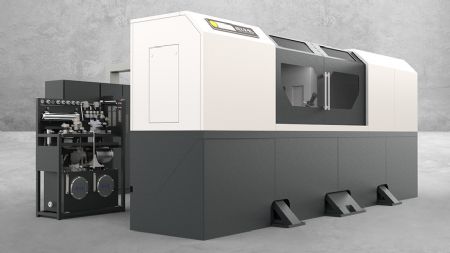
Equipped to mill helical rotors of up to 450mm in diameter, the 4EX-R-BL will also rough mill blower blanks of 320mm in diameter x 900mm in length into straight-fluted rotors in 30min floor-to-floor, ready for finish profile milling to absolute size. This represents a significant time-saving when compared to the 1.5 to 2hr typically required to cut individual Roots-type blower rotor flutes using traditional milling techniques.
PTG Holroyd’s sales director Mark Curran said: “Traditionally, manufacturers producing rotors for Roots-type blowers have relied on NC flatbed milling machines or machining centres that have been retrofitted to absorb the considerable vibrations that occur during the flute milling process.”
Fully automatedWhen you consider that with either one of these production methods each flute has to be milled in a separate operation, it is easy to see why the machining process for Roots-type rotors has historically been labour-intensive. By comparison, the technology offered by both the original and the upgraded 4EX-R-BL moves the manufacture of Roots-type rotors away from traditional flatbed milling — where the component would be manually turned after each flute was cut — to a fully automated, programmable process, able to machine both two- and three-flute blowers in one sequence.”
Removing the need for manual intervention or indexing during the milling of each flute, the Holroyd 4EX-R-BL features a bespoke steadying system that has been designed to withstand the additional forces that are generated during the milling of straight flutes. Specially developed ‘finger clamps’ ensure the workpiece is held securely while a flute is being milled, then release to enable automatic rotation and positioning ready for milling the next flute.
Mr Curran concluded: “In what has been a genuine ‘from the ground up’ revision of a highly successful machine, in the 4EX-R-BL we have a model that is able to produce all helixes from horizontal to vertical, for helical rotors, infinite lead blowers, helical blowers, compressor rotors and vacuum pumps.”