Gas-tight aluminium welding. Photo: TrumpfThe heating system in an electric vehicle (EV) is a complex feat of engineering and crucial to the vehicle’s performance. By using three high-end laser applications, the German automotive supplier
Webasto has taken the manufacture of this vital component to a new level. When purchasing a new EV, you never give a second thought as to whether the heating works — you just take it for granted. However, the heater is not just there to provide a warm and cozy interior, or to clear the windows of frost and condensation in the winter, it also enhances the efficiency of the battery, which operates best within a certain temperature range.
Unlike an internal combustion engine, an electric motor does not produce any waste heat. An EV therefore requires an auxiliary heating system equipped with sufficient power. This uses electricity from the battery to heat a medium – either conventional coolant or battery oil – and thereby deliver warmth. As with any other EV component, the same golden rule applies to the heating unit — ‘the lighter, the better, the smaller, the better’. Leading the way on both these counts is Webasto, the market leader in automotive heating technology.
With its new high-voltage heater, the German manufacturer has now turned up the dial. Designed to function with various EV system voltages and offering continuously adjustable power, this new development also helps stabilise the onboard electrical system. The innovative design and outstanding features are achieved with the use of three laser applications developed in conjunction with high-tech company
Trumpf.
Firstly, ‘gas-tight aluminium welding’ is employed. Jörn Schmalenberg is head of production engineering for the manufacture of electric heaters at Webasto’s factory in Neubrandenburg. This facility produces 95% of the heater components that the company makes for both ICE and electric vehicles: millions of units are manufactured with reliable high-performance lasers and then shipped globally. He said: “An EV heater works like any other heater — you warm a liquid via a heat exchanger and then feed it through pipes. However, liquids and high voltages don’t mix, so it is vital to ensure that the housing is as tight as a drum.”
Disk laserFor this purpose, Webasto uses a lightweight housing made of die-cast aluminum. One way of creating gas-tight welds with this material is to use conventional electron-beam welding in a high vacuum. But this is very expensive and takes too long. Instead, the company uses a disk laser, which can be operated under atmospheric pressure and without a shielding gas. Ideally, this must operate as quickly and as powerfully as possible, the aim being to create a weld seam free of pores. If the laser dawdles at low power, this can cause pores to form in the material as it melts, with the result that the housing will not be gas-tight. He explained: “By using the 16kW TruDisk laser, we are going for the sledgehammer effect, so that there isn’t any time for gas bubbles to form in the first place.”
It is crucial that the laser creates as big a keyhole as possible. Mr Schmalenberg continued: “A lot of laser power gives you a stable keyhole. The more you use, the better it is.” Webasto is very happy with the results right now but is also looking at the new Multifocus optics for this application. This splits the laser beam into four individual spots, which form a square in such a way that their effective radii overlap, thereby creating a very large keyhole. The laser power is spread evenly across the entire area of action, so that the keyhole stays open, without collapsing, and there are no pores.
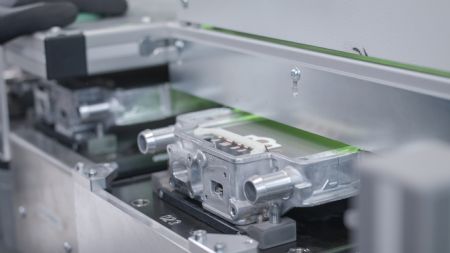
The second laser application is ‘connecting copper with a green laser’. Once the housing has been gas-tight welded, Webasto then connects up the heating elements. As a good electrical conductor, copper plays a key role here. Mr Schmalenberg said: “The mating parts, along with the copper, are highly reflective, which makes laser welding much more difficult.”
Moreover, as with battery cells, the weld seams for the Webasto heating unit must not penetrate too deeply. Otherwise, this could damage the layers below. “We have to be able to precisely regulate the welding depth of the laser. A conventional infra-red laser is of no use here.”
Extremely accurate welding depthsTrumpf’s green laser has a wavelength that is well absorbed by copper. Using the right pulse sequence, extremely accurate welding depths can be consistently achieved – free of spatter and without the need for a shielding gas. The TruDisk Pulse does this with a power of 4kW and pulse durations in the millisecond range. Mr Schamlenberg continued: “We haven’t had a single defect in several million components. That makes everything much more relaxed. We don’t use anything else for welding copper now — just a green pulsed laser.”
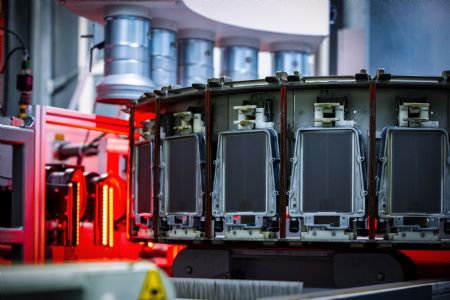
The third laser application is ‘ultraprecise ablation’. Once Webasto is satisfied with the copper welds, attention turns to the actual heating elements. This is where the company’s very own thin-film technology comes into play. Rather than attaching separate conductors, Webasto simply etches them directly into a thin layer of metal. This makes the heater as flat as possible.
Mr Schmalenberg, who uses a TruMicro ultrashort pulse laser for this purpose, explained: “Extreme precision is required when etching the material, so that the laser doesn’t go to deep and damage the layers below. The aim is clean ablation and precise edges. It is vital to avoid any melting, as this can cause defects. The USP lasers take the material directly from a solid to a gaseous state. Without them, we’d be unable to achieve such a flat product design.”
Making the heating unit super flat means it can be installed very close to the components that carry the coolant. Mr Schmalenberg said; “This proximity ensures an extremely fast response time when heating the coolant. What’s more, the special design means that heating power can be almost continuously regulated – both at 400 and 800 volts. We were the first to offer this.”
During voltage peaks, the heater also functions like a small capacitor and therefore helps stabilize the onboard electrical system. Manufacturing in a high-wage country like Germany demands a high degree of automation and innovation. For a company like Webasto, that means using advanced laser technologies. This makes Webasto a preferred partner worldwide. Mr Schmalenberg concluded: “It is safe to say that not many of the EVs produced around the world roll off the assembly line without featuring first-class electrical components from European manufacturers like us.”