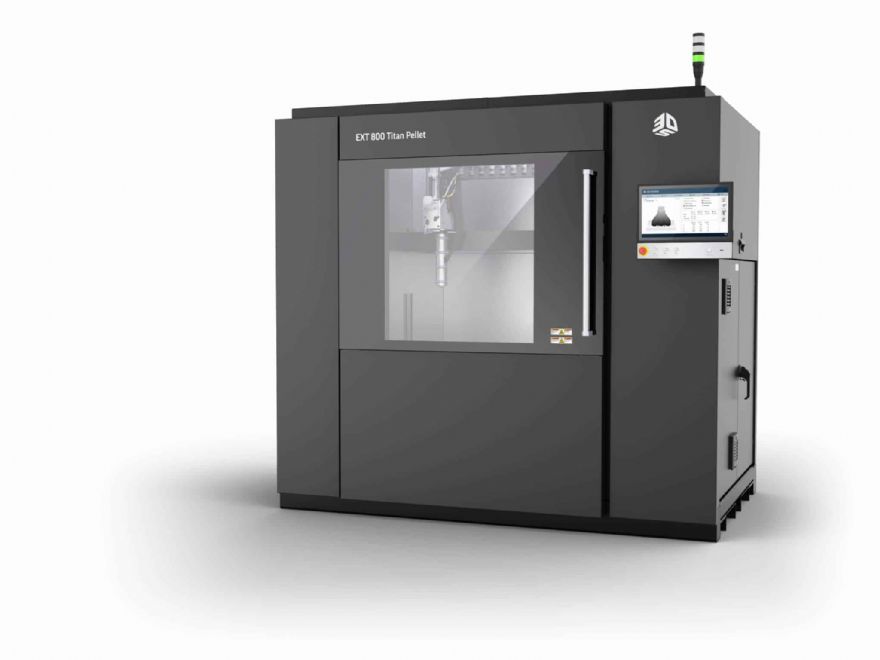
Headquartered in Rock Hill, South Carolina, with offices, manufacturing facilities, and customer innovation centres around the world, the US company
3D Systems recently announced the latest addition to its portfolio of EXT Titan Pellet systems — the EXT 800 Titan Pellet. The company says that with a build volume of 800 x 600 x 800mm, this new pellet extrusion system ‘harnesses the speed, reliability, and efficiency of its large-format EXT Titan Pellet systems (EXT 1070 and EXT 1270) in a more compact format with lower upfront investment.
“As a result, manufacturers can take advantage of the lights-out, production-ready EXT 800 Titan Pellet to fabricate functional prototypes, tooling, fixtures, sand casting patterns, thermoforming moulds, and end-use parts of a more modest size. Moreover, with print speeds up to 10-times faster and material costs 10-times lower than traditional filament-based systems, the EXT 800 Titan Pellet can efficiently and cost-effectively address applications in a variety of markets, including foundries, aerospace and defence, thermoforming, prosthetics and footwear, and research.
Rahul Kasat, 3D Systems’s vice president (Titan), added: “Our EXT Titan Pellet systems are a game-changer, combining high-speed 3-D printing with cost-effective pellets, making the technology ideal for a wide range of applications. Over the years, the customers have asked us for a solution to meet their needs of producing smaller parts with a reasonable production cost. The introduction of the EXT 800 Titan Pellet is designed for manufacturers that are looking for these benefits, but do not need the very large build capacity of our existing systems.
“The EXT 800 Titan Pellet has a single extrusion tool head and is ideal for a wide range of manufacturing environments, including offices, labs, and universities, as well as larger shopfloors. The compact frame enables the 3-D printer to fit through a standard set of double doors providing ease of delivery and installation. The system also includes a large, front-mounted touchscreen for an intuitive user experience.
“Furthermore, active bed and chamber heating allows the use of glass and carbon-filled high-temperature engineering materials such as ABS, PC, Nylons, PEI, and PEEK, as well as highly flexible TPE and TPU that cannot be 3-D printed on filament-based machines.”