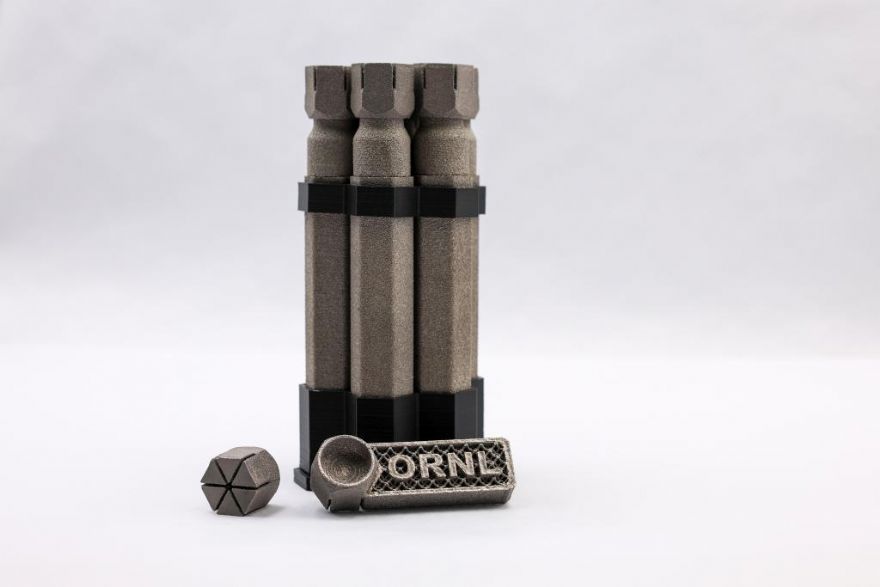
US researchers at the
Oak Ridge National Laboratory (ORNL) in Tennessee, have used electron-beam additive manufacturing (AM) to 3-D print the ‘first complex, defect-free tungsten parts with complex geometries’. It was performed at DOE’s (Department of Energy) Manufacturing Demonstration Facility at ORNL.
The MDF, supported by DOE’s Advanced Materials and Manufacturing Technologies Office, is a nationwide consortium of collaborators working to ‘innovate, inspire, and catalyse the transformation of US Manufacturing; and the researchers at ORNL say the ability to produce these complex tungsten parts that could be used in extreme environments could have positive implications for clean-energy technologies such as fusion energy.
“Tungsten has the highest melting point of any metal, making it ideal for fusion reactors where plasma temperatures exceed 180 million degrees Fahrenheit. In comparison, the Sun’s centre is about 27 million degrees Fahrenheit.
“In its pure form, tungsten is brittle at room temperature and easily shatters. To counter this, our researchers developed an electron-beam 3-D printer to deposit tungsten, layer-by-layer, into precise three-dimensional shapes using a magnetically directed stream of particles in a high-vacuum enclosure to melt and bind metal powder into a solid-metal object. The vacuum environment reduces foreign material contamination and residual stress formation.”
Michael Kirka, a senior researcher and group leader of the Deposition Science and Technology Group at ORNL, concluded: “Electron-beam additive manufacturing is promising for the processing of complex tungsten geometries. This is an important step for expanding the use of temperature-resistant metals in energy resources that will support a sustainable, carbon-free future.”